Inventory Management vs. Warehouse Management
Inventory management tracks stock levels, costs, and item movement, while warehouse management integrates all warehouse operations like picking, packing, labor management, and logistics. Inventory management can be used by any business with stock, whereas warehouse management is specific to distribution centers.
Aspect | Inventory Management | Warehouse Management |
---|---|---|
Definition | Tracks information about items built, bought, stored, or sold. | Manages and coordinates inventory actions and labor scheduling within a warehouse. |
Scope | Focuses on tracking stock levels and movement. | Encompasses all aspects of warehouse operations. |
Complexity | Generally simpler and less expensive. | More complex due to broader functionality and higher costs. |
End Users | Utilized by any business with stock, including small retailers. | Used by businesses with warehouses or distribution centers. |
Features | Inventory tracking, costing, loss analysis, order fulfillment. | Stock control, returns management, labor scheduling, logistics management. |
Automation and Integration | Integrates with inventory tracking methods like barcoding and RFID. | Offers automated order processing and replenishment; utilizes predictive analytics and integrates with various logistics solutions. |
Cost | Generally lower; SaaS options can start at $40/month. | Higher cost; can run into thousands of dollars per user for basic functionality. |
Additional Features | May include basic stock control and demand planning. | Often includes ERP integration, inventory optimization, and third-party logistics coordination. |
Inventory vs Warehouse
What is Inventory Management?
Inventory management, also called inventory control or IMS, keeps track of all information about the items your company builds, buys, stores, or sells. Location tracking assists in picking, packing, and shipping tasks related to inventory movement. Inventory costing establishes the cost value of inventory for profitability tracking and tax accounting.
With an inventory management software, various traceability methods allow you to track stock via barcoding, serial or lot number, and RFID. Detailed recording of on-hand units for each SKU maintains accurate stock levels in real-time. This improved understanding of stock movement can lead to lower operating costs for your organization, as you can streamline tasks such as picking, packing, kitting, and shipping. And with greater visibility into your stock levels, you can minimize instances of loss and theft. This increased awareness of inventory also leads to higher customer satisfaction by determining when fulfillment of customer orders is possible.
Finally, movement histories via location tracking make it easier to conduct forensic inventory loss analysis to determine if there are any obvious areas for improvement. Automated inventory management systems simplify product pricing and maintain the most effective stock levels.
What is Warehouse Management?
Warehouse management system (WMS) software allows managers and laborers to track inventory as it moves across the warehouse floor to the next stop of the supply chain. These systems allow managers to coordinate inventory actions throughout a warehouse or distribution center.
WMS gives warehouse managers powerful tools to oversee workflow, control stock, schedule labor, generate bills, analyze reports, and coordinate with fleets, shipyards, and docks. These systems can automatically log, receive, put away, pick and pack, ship, and report on the products that arrive at your facility. By automating these complex tasks, WMS helps control costs by ensuring items get to the correct destination at a cost-effective price.
Differences vs Similarities
How Are Warehouse and Inventory Management Similar?
Just from the descriptions, there are a lot of similarities between inventory and warehouse management practices. Both are aimed at better controlling inventory, from measuring stock to streamlining movement, through improved practices and advanced automation. They can inform business owners when you need to reorder low stock or schedule replenishment at a specific location. In this way, each plays an important role in overall supply chain management by measuring the flow of products from your warehouse or retail location to the end destination.
Each system can integrate with various inventory tracking methods, ranging from barcode scanning to RFID asset tracking. These traceability options allow you to automatically scan items to gather information rather than manually keying in product data after each shipment or delivery. While RFID readers and tags are gaining popularity in inventory control, hardware expenses need to be considered.
Along with accurate stock via cycle counts, IMS and WMS can use historical data gained from tracking inventory movement to provide analysis for future sales forecasting. Knowing this information can make it clear to managers which products are selling and which are not, allowing for real-time adaptation to changing sales trends.
How Do IMS and WMS Differ?
There are also key differences between these two management systems. To start, an inventory management system can be utilized by any business with inventory, regardless of whether they utilize a warehouse or distribution center for storage. For example, an IMS can be used on a small scale to keep track of products in a backroom at a single retail location.
Warehouse management systems tend to be more complex than inventory management solutions because they don’t just track inventory; they also control every aspect of the warehouse or distribution center itself. Two ways this is evident in WMS are the inclusion of labor scheduling and transportation management, both absent from inventory management software systems.
Which System Do You Need?
If you don’t have a warehouse, you don’t need a WMS. However, if you do have a warehouse, even one with limited capacity, then the choice between an inventory or warehouse management system is trickier.
Warehouse management systems tend to include more features that optimize warehouse operations and inventory. As such, some enterprise-level companies prefer using warehouse management software since it has more comprehensive functionality. It’s important to note some inventory management software systems may include modules for warehouse management, though not always.
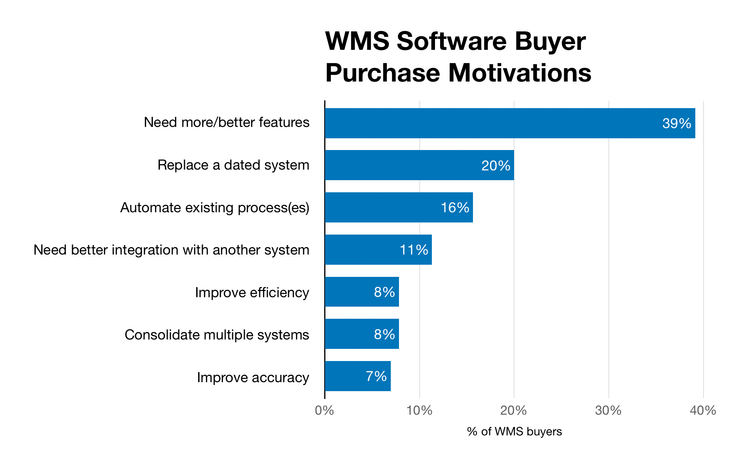
For smaller businesses, inventory management offers many useful tools if you do not need many extras and just want to understand your stock well. Because it is less complex, inventory management software is significantly more affordable than warehouse management systems. Software-as-a-service (SaaS) subscriptions can begin at only $40 per month, compared to thousands of dollars per user for basic WMS functionality.
Other popular solutions that integrate with warehouse management software include:
- Demand planning: Plan ahead for customer demand for goods and services
- Enterprise resource planning (ERP): An integrated suite of business applications designed to automate the back-office functions of your organization, including business processes such as financials, sales, and operations.
- Inventory optimization: Create optimal storage and distribution conditions for inventory
- Sales forecasting: Predict anticipated sales based on past trends and buying habits
- Stock control: Specifically controls onsite inventory, offering more specifics
- Third-party logistics (3PL): Coordinate and oversee logistics of working with third-party warehouses
Consider implementing these solutions along with an inventory management or warehouse management software to optimize your operations.