The Best SPC Software
We picked the top SPC software for manufacturers needing real-time quality control and process visibility. These tools fit a range of needs, whether you’re in automotive, aerospace, or medical device production.
- Streamlines manufacturing operations
- Real-time visibility into the manufacturing process
- Integration with other systems for improved efficiency and productivity
- Several different control charts
- Customizable mobile app
- SAP Digital Manufacturing integration
- Integrates directly with Excel
- Affordable pricing
- Effective statistical tools
Statistical process control or SPC software helps manufacturers monitor quality control data and analyze key process information. Using our advanced review methodology, we’ve ranked our best picks based on data analysis, reporting, and compliance.
- DELMIAWorks: Best Overall
- Minitab SPC: Best for Automotive Manufacturers
- SPC for Excel: Best for Microsoft Users
- Advantive SPC: Best Multi-Site Support
- DataLyzer Qualis: Best for Highly-Regulated Environments
DELMIAWorks - Best Overall
DELMIAWorks’s RealTime Process Monitoring System acts as a live data collection engine, pulling continuous input from machine sensors and factory floor controllers. It captures high-frequency process parameters like injection pressure, cooling cycle times, and defect rates. From there, DELMIAWork’s SPC tools layer on top of RealTime data:
- Dynamic Control Charts: Highlight process drift or out-of-spec conditions; supports X-bar, R, S, p, np, c, and u charts
- Correlation and Cause Analysis: Helps identify root causes of scrap; includes drag-and-drop interface to correlate variables
- Histograms & Pareto Charts: Provide frequency distribution and defect cause analysis
- SPC Drill-Down Reporting: View SPC data by job number, part number, shift, machine, or operator
DELMIAWork’s SPC tools help you catch out-of-control conditions in real time and prevent defective runs later. This SPC software also provides traceable process data for FDA-regulated or ISO-certified environments. It’s a solid fit for manufacturers with $10 to $20 million in revenue who have the technical know-how to install machine-level sensors, especially on legacy or customized equipment.
Minitab SPC - Best for Automotive Manufacturers
Minitab’s Real-Time SPC system delivers strong monitoring and charting capabilities for automotive manufacturers. It offers control charts and dashboards for process monitoring, including Xbar-R, EWMA (Exponentially Weighted Moving Average), and I-MR-R/S. Its advanced control EWMA chart can detect even the smallest process shifts, ideal for auto manufacturers that require precision and tight part specifications.
Its native mobile app allows engineers and manufacturers to look into quality issues from anywhere. The app can automatically send alerts, feedback, and warnings directly to email or text so everyone can stay on top of potential problems that arise. The system is partnered with SAP Digital Manufacturing to allow easy integration with a popular MES. One drawback of Minitab is that it does not have public pricing available.
SPC for Excel - Best for Microsoft Users
SPC for Excel integrates directly with Microsoft Excel, making it accessible and familiar to many users. The software includes many statistical tools, including Pareto charts, control charts, process capability analysis, and Gage R&R analysis.
This SPC software helps users with onboarding by providing training resources like getting started guides and how-to videos, catering to beginners and advanced users. The system starts at $289 for a perpetual license for one user, with discounted prices as the user count increases. This makes the system more affordable than other statistical software packages, making it a good option for smaller manufacturers. However, one downside is that it is only on-premise deployment.
Advantive SPC - Best Multi-Site Support
Advantive SPC (formerly InfinityQS) analyzes several data points, including multiple sites, production lines, and product codes. The granular-level reporting capabilities help manufacturers reduce waste, enhance product quality, and maintain industry compliance.
Additionally, Advantive provides streamlined data collection, housing all collected information in a single data repository for easy analysis. Its control charts deliver real-time insights into any process changes requiring investigation, helping the shop floor stay aware of potential issues. The SPC system easily integrates with other Advantive software, such as its ERP and MES solutions, for complete data control.
5 DataLyzer Qualis - Best for Highly-Regulated Environments
DataLyzer Qualis is adaptable to various industry standards, including FDA CFR 21 Part 11, IATF 16949, and AS13006. This flexibility ensures it can meet the regulatory and quality control requirements of several manufacturing sectors, including automotive and medical parts. DataLyzer also offers integrated OEE, CAPA, FMEA, and MSA for further processing analysis.
Its customizable shop floor screens allow operators to tailor them to their specific needs and create personalized workflows for different data entries. The software supports more than 20 languages, so users can better access locally-based partners worldwide. However, some users have reported trouble saving individual part parameters, which could create tedious data re-entry.
What is SPC Software?
Statistical process control software (SPC software) collects quality and performance data in real time for statistical analysis. Manufacturers use SPC software to identify product quality issues and process variations, take corrective action before extensive issues occur, and improve process performance.
SPC software monitors product quality control data and the performance of machines and other manufacturing tools. It notifies shop floor personnel when product quality or machine performance exceeds the acceptable range. This allows manufacturers to reduce rework, improve efficiency, and increase their bottom line.
The data collected by SPC software is plotted onto user-friendly graphs. Having the data in an easy-to-read format lets you see when data variations occur and how far they deviate from the expected value.
Types of SPC Software Charts
SPC charts give manufacturers a better handle on data management. The raw SPC data is formatted into charts showing product or process quality variations. Some of these charts include:
Control Charts
Control charts are important SPC tools that plot changes in process data over a period of time. These charts typically feature three horizontal lines demonstrating the upper, lower, and average control limit. When data falls outside the control limit range, your team will be notified to take corrective action immediately. You will be prompted to analyze the root cause to determine why the data outliers occurred. This helps you make more informed decisions when taking corrective action.
Control charts within SPC software can be customized to monitor processes relevant to your business, such as temperature ranges or machining time.
There are a few different types of control charts that can be created within SPC software, including:
- X-Bar and Range “R” Charts: Data collected at regular intervals from a small, constant sample size (typically under 10) to determine the minimum and maximum ranges between a set of data points.
- X-Bar and Standard Deviation “S” Charts: Data collected from larger samples to determine variations using all data collected (not just the min and max ranges).
- Individual-X and Moving Range Chart (IX-MR): Data is collected from a single sample size to show individual measurements and absolute differences between values. These charts are typically used when sampling is time-consuming or expensive.
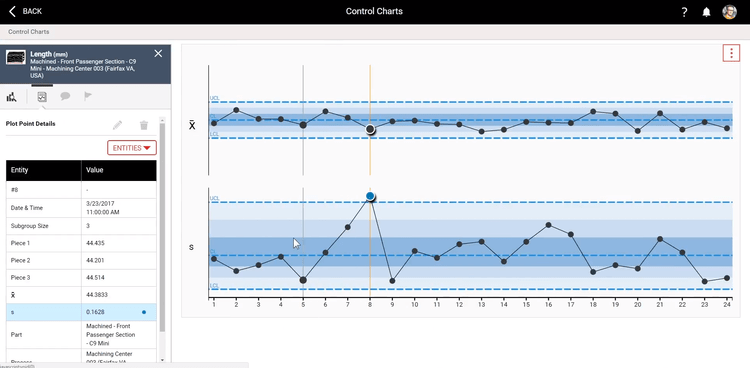
Pareto Charts
SPC software compiles and plots data into a Pareto chart. Pareto charts provide a bar chart of issues or causes of problems and prioritize the issues in order of frequency. This data can include:
- Defect types
- Customer complaints
- Reasons for machine downtime
- Reasons for late deliveries
- Injuries on the job
Knowing where issues are coming from and their frequency helps you prioritize and take corrective action.
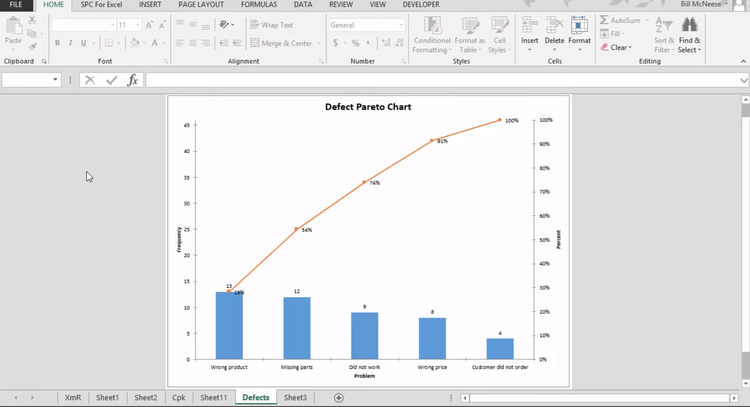
Histograms
Histograms in SPC software are bar charts that show data distribution over time. For example, the SPC software will compile data on bottle diameters for a production run over a specified period of time. The diameter measurements are plotted onto a histogram that allows you to see how many bottles had diameters that were too big or too small.
The shape of the histogram allows you to determine whether the process variations were stable or unstable. Histogram charts are often used in conjunction with control charts to visualize the data distribution more clearly.
What Type of SPC Software Do You Need?
SPC software can be a standalone solution for companies looking to integrate statistical process control into their current system or as part of a complete ERP solution. Some SPC software packages are geared towards manufacturers with industry-specific quality compliance requirements.
Standalone SPC Software
Standalone SPC software is a great option for manufacturers with straightforward production processes that want to focus on quality or process improvement. These solutions are often easily integrated with other existing systems like quality management systems, CMMS, or MES systems for more in-depth supply chain management, waste tracking, traceability, work-in-progress tracking, and more.
Real-time data collected from quality systems and other software products can then be automatically plotted onto easy-to-read charts and graphs. Some solutions work with Microsoft Excel to import and graph the SPC data in a familiar environment.
Industry-Specific SPC Software
Certain manufacturing industries need an industry-specific SPC to ensure their products and processes comply with regulations. For example, the FDA regulates medical device manufacturers to meet certain quality standards to ensure they are safe and effective for patient use. 21 CFR 820:100 dictates that corrective and preventative action (CAPA) processes must be in place. SPC software helps medical device manufacturers track the right quality data and enact CAPA.
ERP Software with SPC Capability
Large manufacturers that want an all-in-one solution to handle a variety of processes like accounting, customer relationship management, budgeting, and statistical process control can look for a complete ERP system. ERP software that is geared toward the manufacturing industry can have an SPC module that provides comprehensive statistical tools for data analysis and continuous improvement.
Primary Benefits
Automatic Notifications
Real-time statistical process control solutions assist with data collection and analysis. When data points fall above or below the expected parameters, the system automatically notifies you as soon as the anomaly occurs. These data points could include temperature ranges, product dimensions, and machining time.
Catching issues as soon as they occur will help you reduce waste and overall production costs. You won’t have to scrap an entire product or production run due to an error that wasn’t caught until after the fact.
Reduced Waste and Rework Time
The data analysis tools in real-time SPC software allow you to make quality improvements to manufacturing processes and products during production. This decreases the amount of wasted material and time spent completely reworking or throwing out defective products. Having reliable quality control data from SPC software will also prevent you from shipping defective products to customers.