The Best Manufacturing Execution Systems (MES)
We’ve reviewed the top manufacturing execution systems (MES) across industries, from electronics to automotive, focusing on features like WIP tracking and rules-based routing.
- Competitive pricing with a "pay as you go" model
- Predictive modeling through AI integration
- Real-time machine monitoring
- Platform is adaptable to wide range of business types
- Implementation takes 8-12 weeks on average
- Offers role-based access
- Gathers real-time shop floor data
- Great customer support
- Logical, intuitive UI
Our MES software picks span industries like food and beverage, chemicals, and pharmaceuticals, offering solutions that boost throughput and minimize cycle times.
- ShiftWorx: Best for Automotive
- ShopVue: Best for Labor Management
- HYDRA X: Best for Food & Beverage
- FactoryTalk: Best for Pharmaceuticals
- Eyelit MES: Best for Aerospace & Defense
- MasterControl: Best for Medical Devices
- FactoryLogix: Best for Electronics
- Epicor Advanced MES: Best SPC & SQC Modules
- Infor MES: Best for Chemicals
- DELMIAWorks: Best for Plastics & Rubber
ShiftWorx - Best for Automotive
ShiftWorx’s scrap and downtime reporting module can help you reduce defective parts and machinery breakdowns during high-volume production. For instance, if machining errors result in defective engine blocks, your operators can log these instantly as “scrap entries.” From the ShiftWorx menu, they can then select reasons like “tool wear” to create traceable data for each issue.
The dashboard then consolidates this information into visual formats, giving you insights into trends over time. Data is layered by:
- Job/Batch: Linking scrap data to specific production orders or part runs.
- Machine: Identifying the equipment responsible for the scrap, like stamping presses.
- Operator: Tracking which employee operated that machine at that time.
Additionally, this MES system records downtime and categorizes it as planned (like routine maintenance) and unplanned (like breakdowns or machine jams). Color-coded indicators on the dashboard help you pinpoint and resolve problem areas.
You can then run reports that correlate downtime events with scrap occurrences; for instance, data may reveal that unplanned downtimes during die changes lead to higher scrap rates during the stamping process. With these insights, you can target inefficiencies and address recurring machine issues.
ShiftWorx offers a “pay as you go” modular system at $125/machine/month or $1,500/machine/year. While startups might find it pricey, it’s a solid option for small to mid-sized companies, especially in automotive manufacturing.
Check out our full review of ShiftWorx for ratings and pricing.
ShopVue - Best for Labor Management
ShopVue lets you focus on both machine performance and employee metrics with its labor tracking tool. Via a streamlined, intuitive console, your supervisors can monitor KPIs like order progress, performance against standards, and labor efficiency.
An operator starts a job or begins a shift by scanning a barcode, which automatically logs them into ShopVue and ties their work to a specific order. As they log time, this MES software performs up-to-the-minute checks. For instance, the system prevents reporting quantities that exceed the order’s expected output, eliminating errors in production tracking. At the end of the job, the operator simply taps “Finish Run,” where they’ll be prompted to enter the number of goods and scrap quantities.
The labor tracking tool includes a number of sub-capabilities:
- Automated Time Tracking: Records attendance and links labor hours to specific orders, eliminating timesheets and simplifying labor cost calculations for accurate job costing.
- Performance Tracking: Displays performance tracking metrics like overall equipment effectiveness (OEE), production yield and scrap, machine efficiency, and utilization on user-friendly dashboards.
- WIP Tracking: Provides real-time visibility into all work orders, including in progress, completed, or delayed statuses, to better allocate labor.
- Error-Proofing via Validations: Leverages built-in validation rules to prevent operators from entering incorrect or illogical data; the system won’t accept scrap quantities disproportionate to the expected output, for example.
Finally, ShopVue’s labor tracking tool integrates with payroll systems like Paychex Flex, utilizing labor data to calculate costs and prepare payroll accurately. Overall, it simplifies job costing and makes labor allocation easier while enhancing your understanding of job profitability. ShopVue starts at $45,000 a year, best for medium to large-sized discrete manufacturers.
See our full ShopVue profile for more info.
HYDRA X - Best for Food & Beverage
HYDRA X’s recipe management module keeps your batches consistent and records effortless. This system handles all the details, like managing raw materials data for everything from ingredients to additives. It then links recipes directly to your ovens and mixers to auto-configure parameters like temperature or speed. This ensures every batch you make meets your quality standards.
On the shop floor, your operators will receive clear, step-by-step instructions with visual indicators for metrics like ingredient weights and target temperatures. It flags any deviations as they occur, allowing your team to fix the issue without disrupting production. HYDRA X also logs every step for full traceability. In case of contamination, you can quickly pinpoint affected batches and trace their distribution.
Additionally, this manufacturing management software adapts to dynamic production needs, maintaining multiple recipe versions for new formulations or seasonal changes. It also scales recipes for different batch sizes without compromising quality and auto-generates FDA-ready batch reports, streamlining inspections and audits. With automated traceability and equipment-level integration, HYDRA X gives you total visibility into your manufacturing operations.
View our full HYDRA X profile for more details.
FactoryTalk - Best for Pharmaceuticals
The electronic batch record (EBR) system in FactoryTalk PharmaSuite streamlines batch release with real-time production data. For example, it integrates weighing and dispensing processes directly into the batch record, making it much easier to monitor material usage. Whether you’re pre-weighing active ingredients or tracking excipients, the software helps you maintain Good Manufacturing Practices (GMP) by enforcing consistent operations and compliance.
PharmaSuite also links data for time- and temperature-sensitive materials to process workflows, critical for producing vaccines and biologics. Through cold chain tracking, you can set thresholds, monitor how product stability, and receive alerts when limits are at risk of being breached. The system automatically records these conditions in the batch record to make compliance and audits much smoother.
Additionally, the software provides standardized master recipe execution. It pulls the parameters and equipment settings needed directly from recipes, then monitors each step in real time. This ensures each step meets predefined criteria before allowing the production process to continue. The EBR system makes it easy to scale up production or transfer recipes while keeping quality consistent.
This MES software is a good fit for large-scale pharmaceutical operations, offering the process controls and advanced compliance these organizations need. While its deep feature set might be overwhelming for smaller companies, it’s well-suited for high-volume facilities with complex workflows and regulatory demands.
See our full review of FactoryTalk to learn more.
Eyelit MES - Best for Aerospace & Defense
Eyelit MES is ideal for manufacturers tackling complex and high-stakes systems. Its end-to-end traceability tools track the complete history of materials, components, and sub-assemblies throughout the production lifecycle. This lets you trace every part back to its source vendor and lot; in this way, the system provides auditable records required for AS9100, ITAR, and MIL-STD standards.
This MES integrates barcode, serial number, or RFID-enabled technologies for real-time tracking, further accelerating your workflows. Whether pinpointing a batch’s location in real time or identifying the source of a deviation, Eyelit provides seamless forward and backward traceability. When defects do occur, the software dynamically reroutes parts or batches through alternate workflows to keep operations running smoothly.
The software integrates with optional modules like Eyelit QMS to offer statistical process control (SPC), non-conformance reports, and corrective and preventive actions (CAPA). This lets you monitor any quality variations and ensure continuous improvement when issues are found. Overall, Eyelit MES helps you resolve problems faster, reduce downtime, and minimize safety risks. However, users have noted occasional glitches and system downtime, though their responsive service team quickly resolves these issues.
Read reviews and learn more about key features for Eyelit MES.
MasterControl - Best for Medical Devices
MasterControl’s electronic device history record (eDHR) module simplifies complex production processes. In compliance with FDA regulations like 21 CFR Part 820, it records every manufacturing step, linking procedures, training records, and quality inspections for a real-time view of operations. This input originates from various systems, like ERP, QMS, or IoT devices, so your data is accurate and accessible.
This system leverages built-in conditional logic to tweak workflows dynamically based on certain outcomes, like passing inspections or flagging quality issues. It also integrates guided work instructions so your operators follow the correct process each time. Progress indicators and KPIs, like initiation dates and batch sizes, keep you informed and on track.
Real-time alerts notify your team if parameters exceed predefined limits, enabling quick fixes to prevent delays. Additionally, this software tracks components and materials throughout the manufacturing lifecycle to ensure complete backward and forward traceability. Lot-level segregation allows you to pinpoint defective or noncompliant products instantly.
Medical device manufacturers benefit greatly from its streamlined compliance and faster approvals. However, users report that MasterControl may be pricier than other eQMS systems, though the developer does not list those details publicly. For a more affordable solution, we recommend ShiftWorx at $125/machine/month.
See reviews and learn more about MasterControl Manufacturing Excellence.
FactoryLogix - Best for Electronics
FactoryLogix includes a CAD-intelligent inspection system for precise, visual quality control tailored to electronic products. Instead of relying on text-based defect descriptions, your inspectors can interact directly with a digital product model to tag issues like solder bridges or misaligned components directly on the CAD representation.
The software integrates with external design tools like AutoCAD to import printed circuit boards and electronic assembly models. You can work with component-level details like pins and traces, mapping issues directly to the product layout. This enhances traceability and helps correlate recurring problems to their origins, driving process improvements and traceability.
FactoryLogix includes a standardized list of codes for common concerns, including:
- Tombstoned components
- Solder dewetting or non-wetting
- Improper mounting height
- Backwards or upside-down components
Non-conforming units automatically route to rework stations, where operators use the same CAD-based interface with highlighted problem areas. These dynamic instructions help minimize errors during rework and ensure consistency in corrections. From there, FactoryLogix tracks the status of each unit, from in-process to fail to scrap, and feeds this data into dashboards to provide live yield rates and KPIs.
This MES is ideal for manufacturing businesses with at least 50 employees. However, due to its complexity and higher starting costs, we wouldn’t recommend it for small businesses or startups.
Check out our FactoryLogix profile for more details.
Epicor Advanced MES - Best SPC & SQC Modules
Epicor Advanced MES offers statistical process control (SPC) and statistical quality control (SQC) for manufacturers in electronics, aerospace, and medical devices. The system continuously gathers data from machines and sensors on the shop floor, including parameters like speed, pressure, and temperature.
The module then pulls this data into dashboards and customizable reports, helping you identify anomalies and process trends. With over 1,000 pre-configured analysis options, you can easily evaluate performance and monitor process stability. One-click drill-down functionality simplifies root cause analysis, letting you pinpoint and address inefficiencies or defects with historical and current data. Additionally, the system automatically rejects or qualifies parts based on compliance with your predefined quality standards, meaning only high-quality components move forward.
Your operators will get notifications when process parameters exceed acceptable control limits so they can act immediately and minimize disruptions. While comprehensive mobile usability is limited, the system does include mobile-friendly tools like the Next Gen Andon module for tracking issues and receiving alerts on the go.
View our Epicor Advanced MES profile for key features and benefits.
Infor MES - Best for Chemicals
Infor MES includes by-product management and traceability capabilities. This is useful in manufacturing processes that yield secondary products or waste materials that require careful tracking, classification, and utilization.
The system accomplishes this by linking by-products directly to their production order or batch, enabling forward and backward traceability. You can then classify these products as reusable, recyclable, or waste for proper handling. Infor MES then streamlines regulatory compliance with standards like EPA, REACH, and FDA by auto-generating detailed labels and documentation for these by-products.
This system goes a step further by tracking energy and resources consumed in by-product processing, helping you allocate costs more accurately. What’s more, Infor MES integrates with ERP systems like Infor CloudSuite Chemicals, enabling real-time data exchange. This means inventory movements on the shop floor, like raw material usage, are accurately reflected in the stock levels and work orders in the ERP for consistent and reliable data across operations.
Get pricing details and more on our Infor MES profile.
DELMIAWorks - Best for Plastics & Rubber
DELMIAWorks’s RealTime Process Monitoring System extracts data directly from machines on your shop floor, including injection molding and extrusion systems. You can even retrofit legacy equipment with its programmable logic controllers (PLCs) and modern sensors.
This system pulls live data on KPIs like part counts and cycle times. It then calculates overall equipment effectiveness (OEE) to pinpoint performance bottlenecks, like machines operating below standard speeds. If any machine exceeds your preset limits for temperature or pressure, the system triggers an alarm and notifies you through email or SMS messages. Additionally, the system includes downtime tracking, providing granular insights into causes and solutions for faster troubleshooting.
DELMIAWorks stores all of these details in a central database, allowing you to review historical runs by shift, machine ID, lot number, and part number. It even offers an SPC module with real-time charts visually mapping machine parameters against quality metrics. For example, you can see how fluctuations in mold temperature affect scrap rates or cycle times, allowing you to adjust your operations as needed.
Setup involves some upfront investment in sensors and technical integration–particularly if you have older or highly specialized equipment. However, it’s an ideal solution for mid-sized manufacturers with around 50-100 employees and $10 to $20 million in revenue. DELMIAWorks is approximately $250 per user per month, with a minimum of five users.
Find out more about DELMIAWorks on our product page.
Other Systems We Like
Fusion Operations (formerly Prodsmart) is an effective and affordable option for small to midsize automotive companies and machine shops. It allows you to visualize workflows and maximize production performance across the entire shop floor.
What is a Manufacturing Execution System?
MES software is a system that enables complete shop-floor control, scheduling capabilities, and continuous improvement through real-time monitoring and corrective actions. Its main goal is to automate the processes necessary to turn raw materials into finished products.
Sometimes known broadly as manufacturing operations management (MOM), capable MES software supports these initiatives:
- Maximization of throughput and resource utilization,
- Decreased manufacturing cycle times,
- Reduction of scrap and rework,
- Minimized inventory holding costs based on just-in-time inventory
- Increased ability to reliably achieve quality targets,
- Improved ability to meet regulatory compliance standards.
Read more: What is MES? Understanding Manufacturing Execution Systems to better understand what really goes into an MES platform.
Key Features & Benefits
Feature | Description | Benefit |
---|---|---|
Change Management | Coordinate alterations to materials, equipment, processes, or supply chain routing. | Ensures agility in adapting to production changes. |
Document Management | Provides paperless, multi-format storage, search, and retrieval for SOPs and CAD drawings. | Streamlines access to critical documentation. |
Downtime Management | Tracks machine downtime via PLC connections and schedules maintenance. | Reduces unplanned downtime, optimizing equipment utilization. |
Traceability | Uses barcode or RFID tracking to monitor parts, batches, or lots. | Improves product tracking accuracy and compliance with regulatory standards. |
Inspection Management | Enables workflow controls for executing quality inspections. | Increases consistency and reliability of quality assurance processes. |
Job Tracking | Provides real-time visibility into job status as it progresses through production. | Improves scheduling accuracy and communication among production teams. |
Labor Tracking | Tracks labor time and attendance against job assignments and dispatching data. | Improves workforce management, ensuring accurate labor costing and allocation. |
OEE Analysis | Measures OEE using performance, loading, and availability data. | Helps improve machine performance and productivity. |
Work-in-Process (WIP) Tracking | Tracks inventory position at all stages of the production process. | Reduces waste and ensures accurate inventory management. |
Integrations
Manufacturing execution systems depend on inputs from various other systems to function properly. They integrate via software APIs or are provisioned as part of a larger software system, such as an ERP platform. These integrations include:
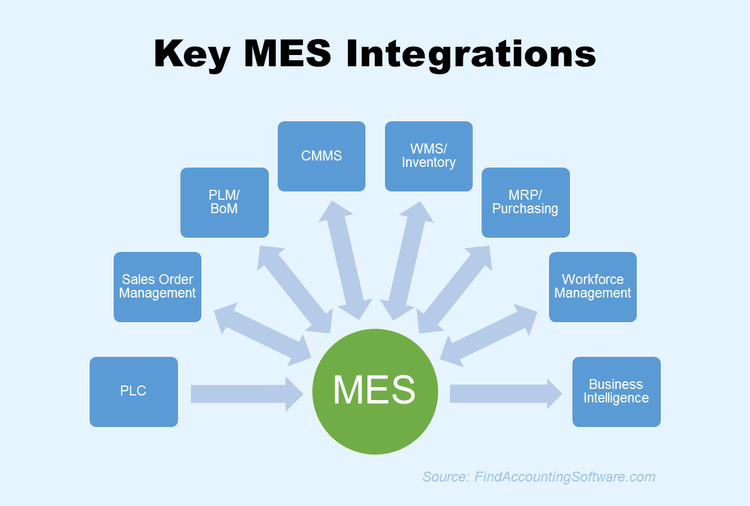
Integration | Functionality and Benefits |
---|---|
Industrial Internet of Things ((IoT) | IIoT devices, like smart sensors, programmable logic controllers (PLCs), and edge devices feed real-time machine data directly into the MES, including equipment status, availability, output, and count. |
Order management | Sales order management systems provide customer requirement details to improve production scheduling; MES updates fulfillment status so sales teams can communicate progress, lead times, and delivery dates to customers. |
Product lifecycle management (PLM) | PLM and bill of materials modules modules deliver data to MES systems to plan manufacturing phases; MES captures diagnostic quality data and feeds it back to improve production processes. |
Computerized maintenance management software | CMMS platforms inform MES software of scheduled equipment downtime; MES collects sensor data on equipment health and sends it back to CMMS to coordinate maintenance events. |
Warehouse management software | WMS and inventory modules supply stock availability data to plan materials and schedule production; MES sends WIP inventory updates back to the WMS. |
Material resource planning (MRP) | MES synchronizes forecasting, materials management, and production using shop floor data to optimize procurement and just-in-time initiatives. |
Business intelligence software | Consolidates business data from various sources and generates reports and visual analysis tools; MES data, such as OEE analytics, throughput, and quality metrics, integrates with BI systems for advanced reporting. |
Workforce management | Leverage labor scheduling and tracking to ensure employee availability; employee performance data captured by MES software feeds into workforce management software to enhance scheduling. |
Implementation Goals for MES
Objective 1: Enhance Quality Management
Introduce real-time machine and process monitoring, adopt digital guidance for tasks, and perform instantaneous quality assessments. This will boost process consistency and product standards while ensuring deviations are documented promptly.
Objective 2: Transition to Digital Manufacturing Operations
Transition from traditional paper-based methods by utilizing digital task guidance, electronic order deployments, and digital record-keeping. This not only reduces environmental impact but also minimizes human errors and consolidates data sources.
Objective 3: Streamline Manufacturing Workflows
Integrate and oversee activities on the shop floor across multiple departments and facilities. By establishing these connections, manufacturing efficiency can be maximized. Utilize live feedback to identify potential problems and swiftly rectify them, further enhancing process effectiveness.
Objective 4: Enhance Equipment Utilization and Maintenance
Monitor equipment performance in real-time, track wear and tear, and schedule predictive maintenance. By doing so, unplanned downtimes can be minimized, the lifespan of equipment can be extended, and overall operational efficiency can be enhanced.
Objective 5: Ensure Compliance and Traceability
With heightened regulatory scrutiny in many industries, MES software can help ensure products are manufactured under prescribed conditions. Capture and store all relevant data, facilitating traceability and ensuring compliance with industry-specific regulations.
Objective 6: Improve Inventory Management and Reduction of Waste
MES can reduce overproduction and excess inventory costs through real-time visibility into inventory levels and production requirements. Additionally, it can aid in identifying and minimizing waste, be it in materials, time, or processes.
How to Choose MES Software
Selecting the right manufacturing execution system (MES) software is vital for improving overall efficiency in manufacturing industries and process industries.
Step 1: Identify Your Industry-Specific Needs
Different sectors have unique requirements. For instance, healthcare may prioritize serialization for regulatory compliance, while the high-tech industry requires seamless integration with IIoT devices and smart sensors to improve precision. Here are our recommended systems for industries most likely to require MES software.
Manufacturer Type | Recommended Systems | Estimated US Market Cap | Key Features |
---|---|---|---|
Food & Beverage | HYDRA X | $1.1 trillion | Recipe management, lot traceability, regulatory compliance |
Chemical Manufacturing | Infor MES | $800 billion | Batch tracking, regulatory compliance, hazardous material handling |
Automotive Manufacturing | ShiftWorx MES | $600 billion | Production scheduling, quality management, traceability, smart mobility solutions |
Aerospace & Defense | Eyelit MES | $500 billion | Compliance management, complex assembly tracking, quality assurance |
Electronics Manufacturing | FactoryLogix | $400 billion | Component traceability, real-time monitoring, defect tracking |
Pharmaceutical Manufacturing | FactoryTalk PharmaSuite | $350 billion | Batch record management, compliance with FDA regulations |
Plastics and Rubber | DELMIAWorks | $100 billion | Quality management, production scheduling |
Step 2: Research MES Products and Reviews
Research MES product reviews to understand leading platforms’ overall performance and key features. Both FactoryTalk ProductionCentre MES and Infor MES support large-scale production environments with multiple plants. Companies like Rockwell Automation and Siemens AG provide tailored MES solutions that leverage cutting-edge technologies. Look for platforms supporting:
- Intelligent infrastructure or real-time monitoring of IoT-connected production lines
- Distributed energy systems or tools that integrate energy usage data with manufacturing operations
You can also opt for software that solves specific issues or simplifies certain operations:
Problem | Feature | Software |
---|---|---|
Reducing defects and downtime in high-volume production | Scrap & downtime reporting | ShiftWorx |
Tracking performance and labor costs | Labor tracking with real-time KPIs | ShopVue |
Ensuring batch consistency & traceability in food production | Recipe management with step-by-step instructions | HYDRA X |
Streamlining pharmaceutical batch release | Electronic batch record (EBR) system | FactoryTalk PharmaSuite |
Meeting aerospace & defense compliance | End-to-end traceability for high-stakes systems | Eyelit MES |
Meeting FDA compliance for medical devices | Electronic device history record (eDHR) module | MasterControl Manufacturing Excellence |
Enhancing QC with CAD-based inspection | CAD-intelligent inspection system | FactoryLogix |
Monitoring SPC & SQC | SPC & SQC modules | Epicor Advanced MES |
Managing chemical by-products and compliance | By-product management & traceability capabilities | Infor MES |
Tracking machine performance in plastics & rubber | RealTime Process Monitoring System | DELMIAWorks |
Step 3: Compare MES Vendors
Vendor comparisons help you assess the strengths and weaknesses of each MES software. Infor, for example, caters to a wide range of sectors, such as medical devices, plastics, electronics, and industrial manufacturing, making it a versatile option. Rockwell Automation and Siemens AG might appeal to large manufacturing enterprises looking for strong automation tools and integration capabilities with their current ERP systems and hardware.
Step 4: Assess Scalability and Cloud Integration
Modern MES software increasingly supports cloud-based solutions, offering flexibility and scalability. Oftentimes, business cloud software lets you start with certain modules and add capabilities as your company grows. Additionally, find integration-friendly systems that can sync with your existing ERP, IoT devices, and supply chain software.
Step 5: Consider Total Cost of Ownership
While upfront costs are important, don’t overlook the long-term value. Factor in expenses for hardware, training, and customizations needed to align the system with your specific workflows. Understand whether ongoing costs include regular updates, technical support, or premium fees for faster customer service response times.
Pricing Guide
MES pricing can vary widely and can be influenced by the number of personnel, machines, and users you have.
Tier | Operation Size | Annual Cost | Example Products |
---|---|---|---|
Low-Cost MES | 1–5 users or 1 production line | $5,000 – $20,000 | Katana, Prodsmart (now Fusion Operations), Fulcrum Pro, Bluestreak |
Mid-Range MES | 6–20 users or 2–3 production lines | $20,000 – $75,000 | ShopVue, IQMS (now DELMIAWorks), MPDV, Eyelit, Aegis, Rockwell Automation |
High-End MES | 21–50 users or 4–10 production lines | $75,000 – $250,000 | iBASEt Solumina, GE Proficy MES, Siemens Opcenter, ShopVue MES |
Enterprise MES | 50+ users or 10+ production lines, multi-site | $250,000 – $2,000,000+ | Rockwell FactoryTalk, AVEVA MES, SAP Digital Manufacturing |
However, most MES developers do not publicly disclose their pricing, so their rates may align with these ranges or even exceed them.