The Best CAPA Software
CAPA software can streamline quality control processes for several industries, including life sciences, food and beverage manufacturers, and pharmaceutical companies. We’ve reviewed the top systems to help organizations of all sizes comply with strict regulations.
- 23 built-in modules
- Suitable for pharmaceuticals, food & beverage, etc.
- Compliant with FDA 21 CFR Part 11
- Provides in-depth audit trails
- High configurability and customization options
- Ready to use best practices
- Customizable dashboards and reports
- Automated notification system
- Responsive customer support
CAPA software is necessary for any business requiring a quality control system. Using our in-depth review method, here are our top picks for the best CAPA software:
- QT9 QMS: Best Overall
- EtQ Reliance: Best Custom CAPA Workflows
- MasterControl Quality Excellence: Best for Life Sciences
- Qualcy eQMS: Strong Compliance Features
- Intellect QMS: Flexible Design Platform
- Greenlight Guru: Best for Medical Device Companies
- Qualio: Good First-time QMS
- AssurX: Most Scalable Solution
- TrackWise: Strong Audit Management
- Qualityze: Best for Salesforce Users
QT9 QMS - Best Overall
QT9 QMS has over 25 built-in modules, allowing you to control all of your quality management processes on one system. Specifically, its CAPA management module has a comprehensive root cause analysis (RCA) tool that helps you analyze underlying sources of events. The system supports several of the leading RCA methodologies, including:
- Five whys
- Fishbone diagrams
- Failure mode and effects analysis (FMEA)
- Pareto charts
The RCA tool is flexible, helping identify problem sources for a wide range of industries, including life sciences, pharmaceuticals, medical devices, food and beverage, and automotive. For example, QT9 can help you investigate machine failures using the “five whys” method to better align with ISO/TS 16949 requirements. You can also apply the FMEA method to investigate patient safety incidents in life sciences. Regardless of industry, the RCA tool will help you stay compliant with standards and regulations by identifying and correcting underlying issues.
QT9 QMS is best for mid to large-sized companies that need an all-in-one system rather than a standalone CAPA software. Pricing starts at around $2,200/user/year with concurrent licensing, giving you access to all 25+ modules.
EtQ Reliance - Best Custom CAPA Workflows
EtQ Reliance’s internal designer tool offers a no-code environment where quality teams, not just developers, can control and adapt the CAPA process. Non-technical users can tweak workflows, add or remove form fields, set required inputs, and define escalation paths, all on a drag-and-drop interface.
This flexibility thrives in complex environments where CAPA procedures vary by product line or region. That’s because the designer tool supports conditional logic, so your staff can branch workflows based on user input or risk level. For example, if a submitted CAPA is low-risk, the system can automatically skip steps like root cause analysis. Meanwhile, high-risk submissions may trigger cross-functional review and formal training assignments.
The designer also lets your team create entirely new corrective action processes from scratch for supplier issues, equipment failures, or cross-departmental inquiries. Each new workflow connects to EtQ’s broader quality system, pulling in source data from incidents and nonconformances. Results feed directly into related applications like Document Control or Training Management, tightly integrating your ongoing quality operations.
Overall, EtQ Reliance is ideal for large to enterprise-level manufacturing companies in sectors from pharmaceuticals to food and beverage. We wouldn’t recommend it for smaller businesses with under $200 million in annual revenue or fewer than 500 employees.
MasterControl Quality Excellence - Best for Life Sciences
MasterControl Quality Excellence’s clinical CAPA module streamlines processes for companies in the life sciences industry. The clinical monitoring tool offers customizable forms and checklists, including source data verification. It even includes forms to document and track protocol deviations. This allows you to log all trial activities for patient safety and compliance with FDA 21 CFR Part 820.
For deviations, you can use the built-in risk matrix assessment gateway to evaluate the severity of impact and its frequency. If either is at unacceptable levels, you can launch a clinical CAPA. The system incorporates the existing information from the deviation form into the new CAPA for a streamlined workflow. This allows you to implement a strong corrective action plan faster.
MasterControl Quality Excellence is built for mid to large-sized organizations. Due to its large feature set, initial implementation can be complex. Small companies looking for a simpler system may want to consider Qualio.
Qualcy eQMS - Strong Compliance Features
Qualcy eQMS has a strong focus on compliance with regulatory standards, specifically in the medical device, pharmaceutical, and biomedical sectors. It fully complies with FDA regulations, including 21 CFR 820, 210, and 211, and supports maintaining ISO 13485 standards.
It also delivers granular security measures regarding role-based identification, login, and access control. The system’s ability to track document changes with detailed audit trails and its support for electronic signatures with timestamps for document approval further enhance its compliance capabilities.
Intellect QMS - Flexible Design Platform
Intellect QMS’s no-code compliance approach enables customization and the creation of apps, workflows, and reports using drag-and-drop and point-and-click technology. This allows users to tailor the platform to their specific processes without needing extensive technical knowledge. The platform also includes pre-built apps for quality management, environmental, health, safety, and quality (EHSQ) software, among others.
Intellect QMS supports ISO, FDA, and GxP best practices, making it adaptable to many regulatory requirements. Additionally, Intellect QMS leverages AI-driven insights to enhance decision-making and operational efficiency, offering a significant advantage in managing quality and compliance tasks efficiently.
Greenlight Guru - Best for Medical Device Companies
Greenlight Guru provides a library of audit-tested SOPs and templates, assisting in creating necessary documentation and ensuring compliance with FDA regulations. It also provides a validation package that simplifies compliance with FDA 21 CFR Part 11, making it easier for companies to assure compliance with evolving validation requirements.
Additionally, Greenlight Guru Academy offers extensive learning opportunities for MedTech professionals. With over 300 curated courses, the academy facilitates continuous learning in the latest trends, regulations, and best practices.
Qualio - Good First-time QMS
Qualio is a good first QMS for smaller companies. In addition to being affordable and scalable, Qualio’s training management system ensures that employees are compliant with SOPs. It includes role-based training functionality, audit trails, and FDA-compliant digital signatures, which are vital for demonstrating compliance during audits.
Qualio focuses on ease of use, collaboration, and compliance with FDA cGMP. It offers features like user-friendly searches, integration with other quality processes, automated reminders, and FDA-compliant digital signatures.
AssurX - Most Scalable Solution
AssurX complies with standards such as 21 CFR Part 820, CGMP Regulations, 21 CFR Part 11, EU MDR/IVDR, and ISO 9001/13485. This wide-ranging compliance capability makes it suitable for diverse industries and scalable for growing regulatory demands.
As a low-code platform, AssurX allows easy customization adaptable to specific business needs. This flexibility is crucial for scalability, as it enables businesses to modify and expand the software’s capabilities in line with their evolving requirements.
TrackWise - Strong Audit Management
TrackWise includes sophisticated audit management capabilities. One of the key strengths of TrackWise is its ability to automate many types of audits, including internal, third-party, and regulatory audits. The software’s workflow engine streamlines every step of the audit process, which eliminates the inefficiencies associated with paper-based audits.
As part of the TrackWise Digital quality suite, the audit management software is fully integrated with other processes like complaint management, CAPA, supplier quality, change control, and document and training management. This integration offers a more comprehensive approach to managing the entire quality and audit lifecycle.
Qualityze - Best for Salesforce Users
Qualityze EQMS is one of the only CAPA systems built on the Salesforce platform. Its cloud-based infrastructure ensures scalability, security, and compliance, making it suitable for numerous sizes and types of organizations. Qualityze’s Salesforce Consulting Services offer tailored solutions, expertise in Salesforce implementation and customization, and support for various Salesforce clouds like Sales Cloud, Service Cloud, Marketing Cloud, Commerce Cloud, Community Cloud, and Einstein Analytics.
What is CAPA Software?
Corrective and preventive action software (CAPA software) is a continuous improvement tool that collects and analyzes data to identify and eliminate product quality issues, process inefficiencies, and equipment issues. Corrective action in software prevents nonconformities from recurring by eliminating the cause of a nonconformity, while preventive action prevents nonconformance from occurring at all.
CAPA software provides risk assessments, alerting you to any potential issues that might arise. This allows you to make changes as needed before a problem occurs. When issues occur, the software will assist with root cause analysis to determine why the issue happened and what can be done to fix it.
CAPA software is used by any business that uses a quality control system. The most common use case for CAPA software is by manufacturers that need to ensure their processes and products meet regulatory standards for their industry.
CAPA management systems are typically integrated as part of a larger quality management system instead of being sold as a single standalone solution. The CAPA system can use data from various parts of the quality system including customer complaints, document management systems, and audit management systems.
Key Features
Feature | Description |
---|---|
Root Cause Analysis | Identifies the underlying problem with a product or process. |
Corrective Action Planning | Defines tasks that will correct noncompliance or issues with a product or process. |
Risk Assessment | Identifies potential problems with product quality and processes. Create preventive action plans to mitigate risk. |
Reporting | Creates reports on the entire CAPA process including errors reported, risk assessment results, CAPA workflow tasks completed, real-time equipment performance, customer complaints, and more. |
Benefits
Identify Product and Process Issues
CAPA management software helps identify and define the underlying quality issue or process failure. The software will alert you in real-time when an issue occurs and provide you with details about what may have caused the problem. More details about the error can be recorded within the software in case the same issue recurs.
Root cause analysis assists personnel with the creation of corrective action plans. Knowing when, where, and why a problem occurred makes it easier to quickly correct it and reduce downtime. This information is then used as the base for corrective action planning.
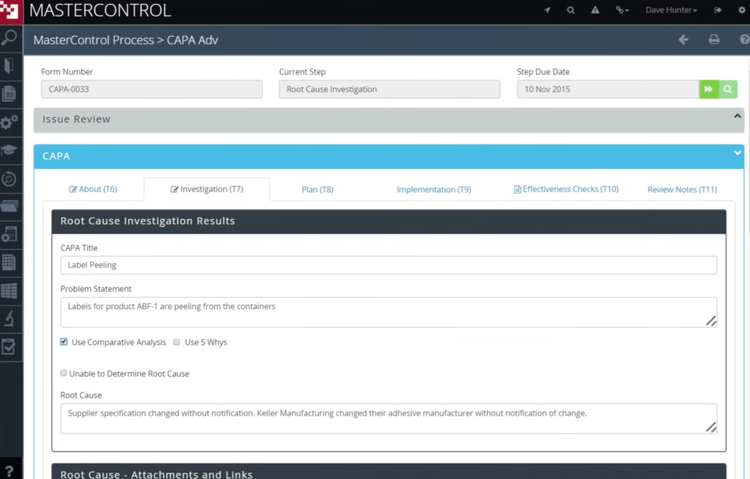
Create Plans to Fix Product Quality
Corrective action software facilitates the creation of corrective action plans. A corrective action plan is a set of instructions that need to be followed in order to correct an issue with product quality or performance. Information from a root cause analysis is most typically used to create a corrective action plan. CAPA software also allows you to assign qualified personnel to tasks with the corrective action plan.
Information from audits can also be used to create corrective action plans. If a process or product quality issue is discovered from an audit and doesn’t meet regulatory requirements, the problem must be corrected immediately. The corrective action plan will define the steps that need to be taken to fix any issues and due dates for the corrections. CAPA software will document the actions taken for follow-up audits.
Corrective action plans are also useful outside manufacturing processes and product quality corrections. For example, corrective action plans can be made for employee performance improvements. The plan will define expectations and steps to take to improve performance.
Reduce Risk and Prevent Quality Issues
CAPA software records data from risk assessments to determine if any problems will occur during or after the manufacturing process. The information gathered from the risk assessment can then be used to create preventive action plans. These plans define the steps to take to prevent a problem with a process or product from happening.
The software can monitor various types of risks including financial risks, operational risks, human resources risks, and more. When potential risks are found, the software will notify you to take preventive action. Risk assessments can be scheduled within the software to occur as frequently as you want.
Gain Insights Into Quality Issues and Potential Risks
Reporting functionality in CAPA software gives businesses valuable insights into problems and potential risks that could negatively impact a company’s ROI, compliance status, and reputation. A few of the areas reports can be run on include risk assessment results, root cause analysis results, corrective and preventive actions taken, equipment performance, and more. The information can be laid out in dashboards, providing you with an easy to use graphical representation of your data.
When your CAPA solution is tied together with a quality system, you can also run reports on other metrics like customer complaints and audit results. Having this information together in one system allows you to have better control over your CAPA processes.
Maintain Regulatory Compliance for Your Industry
CAPA software helps manufacturers maintain regulatory compliance. Different CAPA solutions can be geared towards different industries like medical device manufacturers, life sciences, food and beverage manufacturers, and automotive manufacturers. Certain products need to meet specific quality standards in regards to physical makeup or size specifications. Packaging and labeling can be required and strictly regulated. CAPA software can help manufacturers take the proper steps to ensure their business is meeting all regulatory requirements. If a step is missed at any point in the manufacturing process, the system will alert you to take action before a problem occurs.
Some regulatory compliances that CAPA systems can assist with include:
- ISO 9001
- GMP
- FDA Title 21 CFR Part 11
- HAACP
- IATF 16949
Pricing Guide
We’ve seen CAPA software costs range from $24/month/user to $50,000+ per year. Of course, there are many solutions that fall within this range. The cost of CAPA software varies greatly depending on a number of factors, including the type of software, the number of users, and software deployment. Many solutions offer a free trial period for you to test out the product before committing.
On the lower end, a solution like SafteyCulture (iAuditor) starts at $24/month/user and helps with audit management, corrective action tracking, and team collaboration. This solution is meant for assisting businesses with their auditing process, but we only recommend this if you need basic functions only.
On the higher end, a full quality management system can cost over $50,000/year for large businesses. For example, QT9 QMS starts at $2,000/year/user and includes features like nonconformance management, CAPA management, change management, audit management, complaint management, and more. Full QMS solutions are ideal for businesses that need to manage all quality processes. However, most require you to receive a custom quote for exact prices.