What is Catch Weight Management?
Catch weight management is the process of managing products that have varying weights and quantities. For companies that deal with certain food or other variable-weight items, supporting strong catch weight management in your food distribution software is critical. When you buy in bulk and your end product weight varies, capable catch weight management is a precondition for effectively managing business processes (i.e., controlling inventory, managing cost, minimizing taxes, and accurately invoicing customers).
Read on to learn more about when catch weight management is required, view examples, and compare products that support it.
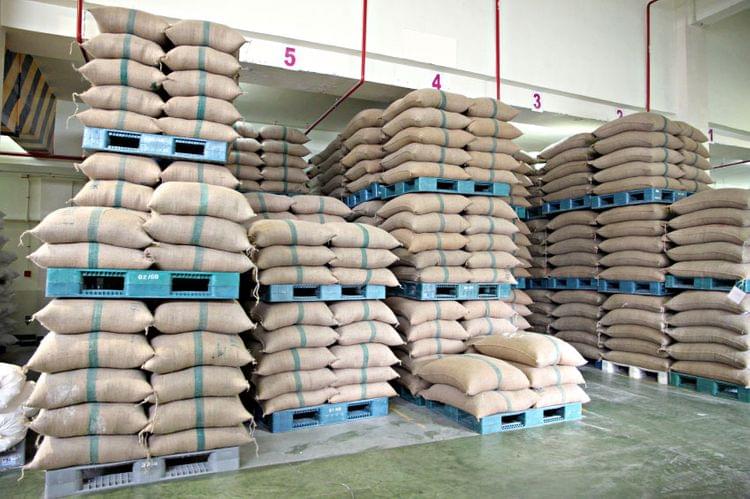
What Is Catch Weight Management?
To put it simply, catch weight management is a tracking approach that allows for the identification of both an average per item quantity/weight as well as an actual per item quantity/weight.
The idea of an “actual per item quantity” seems to make sense on the surface. But the additional requirement for an “average per item quantity” tracking metric might raise the question: Why would you need to use an average versus an exact weight? An example can help illustrate this.
Example of Catch Weight Management
Consider a sample order process that relies on catch weight management:
Step 1: Receive the Order
Your customer calls about ordering a 12-count case of frozen turkeys. You don’t know which turkeys will be shipped, as your warehouse workers will pick the case when the order is ready. However, you can let your customer know that the average weight of a turkey is 15 lbs, and they will be billed $1.50 per pound, with the total invoice based on the exact weight of the shipped case. The estimated cost is $270 for the expected 180 pounds of turkey. That sounds great to your customer, who gave the order the green light.
Step 2: Provision the Product
You internally relay the order for a case of turkeys to the warehouse. Your warehouse selects a specific case of turkeys to ship. The turkeys are weighed, and you’ve got a set of slightly skinny turkeys. The total weight is discovered to be only 150 pounds rather than the estimated 180. This is not a problem with catch weight management. That’s still well within the reasonable range to meet your customer’s expectations, and the turkeys are shipped.
Step 3: Bill the Customer
Knowing your customer would be displeased to pay for 30 pounds of turkey, they did not actually receive, you leverage your catch weight tracking system to bill the customer based on the exact weight rather than the original estimate derived from the average weight. The cost of 150 pounds of turkey works out to $225, reflected on the final invoice sent to your customer.
Catch Weight Inventory Illustrated
It might seem strange that an inventory unit can have multiple weights listed. However, catch weight management is required because the average weight of a unit may differ from the exact weight on an item-by-item basis. Consider how catch weight tracking would lead to different average and exact weights for the same case of turkeys.
That’s catch weight management in action—not so tricky after all. Again, the basics of catch weight management entail a dual quantity inventory tracking system that allows for the data storage of an exact and average weight.
Side note: You’ve likely heard the terms “catch weight” and “nominal weight” used more often than “average weight” and “exact or actual weight.” Actual weight is the same as catch weight. And average weight is often referred to as the nominal weight.
When Is Catch Weight Management Required?
Catch weight management is a common requirement for food and beverage manufacturers, distributors, and retailers. In fact, any company that needs to convert from a relative quantity (eg, case, box, carton, pallet) to a line item price determined by exact weight is a likely candidate for catch weight management.
However, unit-of-measure conversion scenarios are not the only instances where catch weight management comes into play. Some products are indeed purchased in the same unit as they are sold. But, due to processing or environmental factors, unit weight may decrease between the time the item is sourced and brought to market. For example, grain suffers some shrinkage due to evaporation throughout storage.
Products That Support Catch Weight Tracking
Because of the importance of catch weight management features to many manufacturers, distributors, and retailers, a wide variety of products support the feature. Some of the most popular include:
Product | Developer | Target Market |
---|---|---|
S2K Enterprise | VAI developer website | Not industry specific |
FreshByte | FreshByte developer website | Food distributors |
Entree | NECS developer website | Food distribution |
Aptean Process Manufacturing ERP Ross Edition | Aptean developer website | Food and beverage manufacturers |
Epicor Kinetic | Epicor Software developer website | General manufacturing |
SYSPRO | SYSPRO developer website | General manufacturing and distribution |
Acctivate Inventory Management | Acctivate developer website | Product-based distributors |