What is Material Requirements Planning (MRP)?
Material requirements planning (MRP) is a system that calculates the materials needed to manufacture a product and meet consumer demand. Manufacturing companies also use varying types of manufacturing ERP software for production and inventory control. These manufacturing businesses stay profitable by being able to maintain their demand as well as establish priorities in their current processes. In order to accomplish this, business owners have to ask themselves:
- What kind of material will be needed?
- How much material will I need?
- When will I need the material?
Enter MRP, which enables manufacturers to take greater control over the manufacturing process and overall supply chain management.
What is Material Requirements Planning (MRP)?
Material requirements planning (MRP), also known as manufacturing resource planning systems or MRP II software, helps streamline the manufacturing process through production planning, scheduling, and inventory control. Known as a leading type of manufacturing software, MRP systems allow manufacturers to plan and calculate material requirements, coordinate personnel and machine workloads, and optimally plan purchasing to meet customer demands.
MRP also aids in inventory and production schedules to produce products and complete manufacturing jobs. An MRP system determines which assemblies must be built, what materials must be purchased, and the order in which to build products to meet customer due dates.
Through the use of material planning tools, MRP works by taking inputs of material costs, material availability, expected demand, forecasting demand, staffing ability, and machinery capacity–all to ensure your business can satisfy the market as well as your own production goals.
MRP software can work for all types of companies in the manufacturing industry, including make-to-order, engineer-to-order, and discrete manufacturing processes.
How Does Material Requirements Planning (MRP) Work?
Material requirements planning enables manufacturers to control the manufacturing process and overall business processes. MRP systems can create purchase requisitions and initial production requisitions for the purpose of accelerating the manufacturing production process. By determining the raw materials, components, and subassemblies needed, MRP will crosscheck that data with the best time to assemble the finished goods, given the current demand and bill of materials.
In short, an MRP system determines:
- What is needed
- How much is needed
- When it’s needed
What are the Main Steps of a Material Requirements Planning (MRP) Process?
The MRP process can be divided into a number of steps:
- Master production schedule: This enables manufacturers to estimate demand and determine what quantity of dependent demand products and materials are needed and when–accounting for resource, staffing, and inventory needs in order to complete and optimize production.
- Purchasing Planning: Accurately estimate the number of components and raw materials that must be purchased to complete manufacturing projects. If not enough of a product that is needed is available, additional orders will be placed.
- Demand Forecasting: Determine future net requirements of materials and/or components needed to fulfill orders and thus deplete inventory. By taking planned orders into account, a product’s lead time can be shortened, and production downtime can be avoided. Can include inventory reservation and availability management.
- Bill of Materials: A document that specifies the raw materials, parts, and sub-assemblies needed to manufacture a product. Includes precise instructions on what is needed for each production job and breaks down the manufacturing of an item to the component level.
How is Material Requirements Planning (MRP) Used In Manufacturing?
MRP systems in manufacturing environments help decrease inventory through more efficient scheduling, purchase planning, and demand forecasting. MRP will focus on what materials are required to complete manufacturing jobs and when they need to be sourced. This is helpful to minimize stock-outs and reduce excess stock.
One of MRP’s most critical inputs is the bill of materials, or BOM. The BOM is a detailed list of needed raw materials, components, and assemblies in order to manufacture a product. Bill of materials are usually created via order entry systems, reading current inventory levels, and viewing master production schedules.
Bill of materials (BOM) includes hierarchical lists with a top-level representing the finished product and sub-assemblies below it. BOMs can also have two levels of assembly. One example could be a clock that includes the internal clockwork as well as the outer casing.
MRP usage in manufacturing, primarily via a clear and understood bill of materials process, will help you complete each manufacturing job while eliminating waste in materials and better coordinating machine usage and labor.
What are the Benefits of a Material Requirements Planning (MRP) System?
Material requirement planning can be thought of as a manufacturing management system. The shift between MRP I and MRP II was when MRP started to provide additional functionality for manufacturing that included finances, demand forecasting, and machine/labor capacity planning. This allows MRP systems to offer an increasing number of benefits to its users, which include:
- Manage Resources: Ensure raw materials are available, plan equipment usage to avoid machines remaining idle, and ensure assets are being maintained properly.
- Real-Time Inventory Management: Have a clear view of stock levels and maintain minimum and maximum inventory to prevent stock-outs and avoid interruptions to your supply chain.
- Purchase Planning: Track production steps and identify needed purchases while cross-checking with expected material deliveries related to other jobs on your production schedule.
- Document Management: Process and document purchase data, inventory control data, deliveries, cash flow, and more.
- Production Planning: Avoid bottlenecks in the production line by allowing MRP to reroute production or recommending manufacturing an alternative product that has the needed materials available.
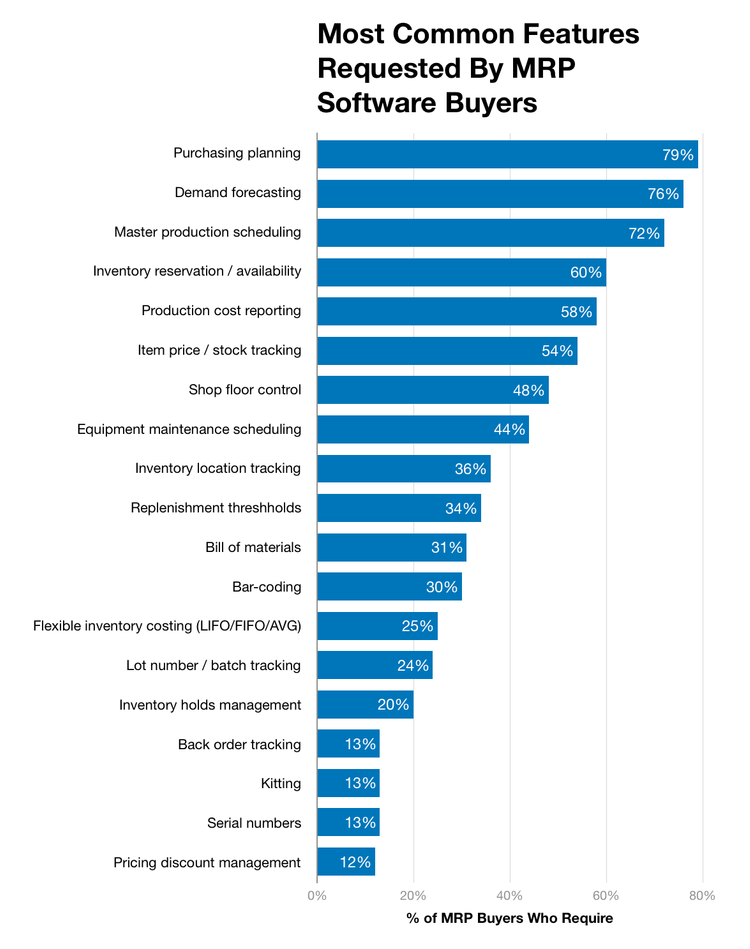
What Is The Difference Between Material Requirements Planning (MRP) and Enterprise Resource Planning (ERP)?
ERP and MRP systems have several key differences. For one, enterprise resource planning, or ERP, is a direct descendant of material resource planning. When MRP II began to include more components of the entire organization (such as equipment maintenance scheduling, accounting and financial planning, and demand forecasting), ERP stepped in to include project management, staffing capabilities, and more.
ERP systems are historically and commonly used by manufacturing and distribution companies. However, the term has expanded to apply to any organization from any industry that is looking to use data from customer demand to help manage staffing and inventory levels.
Today, many software companies may use the terms interchangeably. MRP has expanded to encompass much more than materials, but the core functionality remains unchanged: identify the needed materials, the quantity required, and when they are needed.