The Best Advanced Planning and Scheduling Software
Advanced planning and scheduling (APS) helps manufacturers optimize production by allocating resources and syncing workflows. We tested and reviewed leading platforms to boost visibility, ensure timely deliveries, and reduce waste.
- On-premises only solution
- Reduce inventory and supply costs
- Ideal for discrete part and batch manufacturers
- Cloud or on-premises
- Full ERP solution with APS tools
- Built for manufacturers
- High quality scheduling and sequencing output
- Responsive customer support
- Leverages AI, ML, and optimization to deliver solutions to our clients.
We’ve examined the top APS systems, factoring in usability, support, scalability, security, value, performance, and the range of features offered.
- TACTIC: Best Overall
- Kinetic: Best End-to-End Solution
- Optessa: Best for Global Manufacturers
- FEDRA: Best for Energy Demand Planning
- Visual Planning: Most Intuitive Scheduling
TACTIC - Best Overall
TACTIC is an APS software that integrates with your existing ERP or MRP to improve its scheduling capabilities without requiring a full system overhaul. It specializes in finite capacity scheduling, ensuring your product plans are a reflection of actual shop floor conditions rather than its theoretical capacity.
TACTIC offers tools for:
- Multi-level BOM Scheduling: Plan production across complex product assemblies and subassemblies to reduce idle times.
- Material and Capacity Planning: TACTIC doesn’t just put jobs into any open time, it checks material availability, lead times, and route dependencies before scheduling a job.
- What-If Analysis: Simulate alternate schedules with different constraints, priorities, or assumptions. Then, the outcomes can be compared side by side before committing to production changes.
TACTIC is particularly strong for engineered-to-order (ETO) and made-to-order (MTO) manufacturers where variability between jobs and bottlenecks are common. However, it lacks cloud capabilities and requires on-premise installation, which may be a deal breaker for some organizations.
Kinetic - Best End-to-End Solution
Kinetic is an ERP software for manufacturers looking for APS capabilities along with a full-featured platform to manage operations from quote to cash. Unlike the previous system TACTIC, Kinetic can replace existing systems as it manages your financials, inventory, production, quality, and customer management on top of advanced planning and scheduling.
One of the standout features of Kinetic’s APS module is its Advanced Scheduling Workbench. This virtual workbench gives production planners drag-and-drop control over work orders, visibility into capacity constraints, and automated adjustments based on material availability, shop floor feedback, and job priorities. Kinetic accounts for both setup times and production sequencing, making it ideal for high-mix environments where the goal is not just speed, but reducing disruption to the production workflow.
Because Kinetic is a full ERP, smaller shops may find its all-in-one capabilities excessive for lightweight APS needs. However, for mid-sized to large discrete or mixed-mode manufacturers needing operational control without relying on third-party integrations, Kinetic is a great option to consider. Pricing is quote-based and typically involves per-user licensing ranging from $4,000 to $20,000 monthly, making it an investment for growing manufacturers.
Optessa - Best for Global Manufacturers
Optessa includes a scenario management tool that helps assess “what-if” scenarios across multi-location operations. Using visual dashboards, you can tweak variables like equipment downtimes, raw material delays, and sudden changes in demand. This allows you to evaluate potential impacts before bottlenecks arise and disrupt production.
Key dashboards include:
- Penalty by Constraint Type Chart: Categorizes scheduling penalties, such as inventory shortages or job time window violations, so you can identify the root causes of bottlenecks; allows you to reallocate resources and adjust task priorities to maintain production flow.
- Annealing Dashboard: Charts penalty reductions over time using optimization algorithms; this guides you to better throughput without breaking compliance constraints or delivery commitments, ensuring your operations remain efficient under changing conditions.
Additionally, the tool incorporates demand analysis capabilities to model fluctuations across key attributes like part numbers and color variants. This integration with the broader supply chain helps you manage output levels and order allocation without risking stockouts or overstocks.
This software starts at $5,000/month, ideal for automotive, electronics, and food and beverage manufacturers. While some users report challenging navigation and long run times, it’s adept at intelligent planning for global manufacturers.
FEDRA - Best for Energy Demand Planning
FEDRA is a modular APS platform developed by MPDV, the creators of HYDRA X. One of its standout capabilities is energy demand planning, which integrates real-time energy consumption data directly into the production schedule to help avoid peak loads. This can help you align energy usage with operational or sustainability goals.
Because FEDRA is modular, manufacturers can start with basic finite scheduling and expand over time by adding capabilities like predictive material planning, integrated workforce planning, and quality-driven scheduling. This flexibility makes it a strong fit for growing and digitally maturing operations that want to scale their APS functionality without overhauling everything.
FEDRA is particularly well-suited for energy-intensive industries such as automotive, food processing, and medical device manufacturing, where energy costs and regulatory compliance are critical. However, due to its modular pricing structure, smaller manufacturers with just basic needs might find it cost-prohibitive. In contrast, others will appreciate that they can add on modules as they need.
Visual Planning - Most Intuitive Scheduling
Visual Planning is a scheduling and resource management platform built for usability. Its drag-and-drop interface, color-coded timelines, and real-time collaboration tools make it especially effective for teams that need flexible, visual planning without deep technical training.
Users can quickly assign labor, machinery, and materials to create detailed production plans. Additionally, the system helps track inventory of raw materials, work-in-progress, and finished goods to ensure resources are available and ready when needed by production.
While Visual Planning isn’t a traditional APS in terms of algorithmic depth that other systems offer, it’s a solid fit for manufacturers, construction, and field service organizations with straightforward scheduling needs. It’s ideal if you value speed and accessibility over constraint-heavy optimization. The system has multiple user plans offered at a monthly or annual rate, so you can build a perfect fit system. However, if you require additional customization, expect setup costs to start at $5,000, which scales for larger projects.
What Is Advanced Planning and Scheduling (APS) Software?
Advanced planning and scheduling (APS) software helps manufacturers allocate raw materials, labor, and machine capacity to meet demand with maximum efficiency. Unlike traditional MRP or ERP planning tools, APS systems are built to handle real-world constraints, such as machine availability, setup times, labor shifts, and material lead times, so production plans are both realistic and optimized.
APS solutions generate production schedules that minimize downtime, reduce lead times, and improve on-time delivery rates. Visual tools like Gantt charts, load balancing views, and real-time dashboards give planners the ability to identify ideal start times, machine assignments, and workforce availability across every job and resource on the shop floor.
By syncing your sales, purchasing, production, and inventory data, APS software supports smarter decision-making across both long-term planning and short-term scheduling. It continuously updates production schedules based on changing demand, late material deliveries, or shop floor disruptions such as sick employees or equipment maintenance. This level of responsiveness helps manufacturers stay agile and maintain consistent output under shifting conditions.
The planning part of APS software considers the long term, while the scheduling part considers the short term.
- Planning aggregates the forecast and the supply and divides them into time slots. The objective is to determine what to make or produce in each time slot, how to make it, and how much to make.
- Scheduling sequences the jobs and creates a list that is released to the shop floor while honoring any and all constraints.
Key Features
- Demand Planning: Collects historical data on order volumes and inventory turns and mixes it with continually updated forecasts from separate business units (primarily sales, marketing, and operations) to make more informed supply chain decisions.
- Production Scheduling: Generate resource and material-constrained schedules. Determine the need for materials and capacity to complete a manufacturing production order. Includes drag-and-drop capabilities for “what-if” analysis.
- Constraint Management: Includes visual identification of activities that are delayed due to resource capacity and/or material availability limits (capacity and material bottlenecks).
- Order Management: Captures, tracks, and fulfills orders across multiple sales channels by connecting inventory and sales orders, creating shipping schedules, tracking fulfillment, and creating reports. It also includes alerts, pegging views, statuses, and watches.
- KPIs: Includes impact analysis and analytics surrounding your order management, capacity, productivity, and financial commitments.
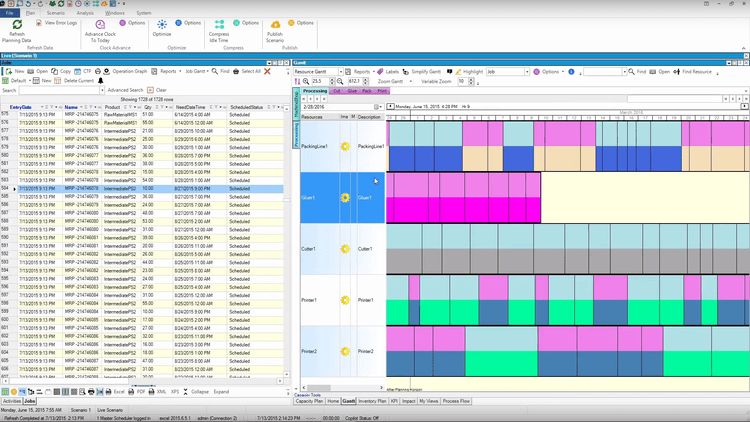
Benefits
Advanced planning and scheduling software solves the issues of:
- Late deliveries due to manufacturing delays
- Missed sales due to demand exceeding capacity
- Lost orders due to excessive work-in-process
- High production costs due to machine ineffectiveness (such as downtime)
- Excessive overhead due to managing scheduling changes and the impact on the delivery schedule
- Difficult to plan for future capacity requirements
The more resources you have to manage, the more overwhelming the planning and scheduling process becomes. Each business will have different ideas of what benefits they want out of advanced planning and scheduling software. In reading some of the top benefits of APS software, businesses should find out how flexible the solution needs to be (does it need to be rigid with predefined features, or can you live without some benefits while you address key concerns?).
Improve Your Manufacturing Process with APS Software
Advanced planning and scheduling software will help you generate manufacturing or purchase orders to satisfy your demand. This goes hand in hand with creating production and purchase plans to ensure you can meet any current or anticipated demand.
APS software will also provide better visibility into your inventory. Visual charts and inventory grids can help identify shortages in your inventory, which can alert staff to reorder or even trigger an automatic reorder point. Likewise, excess inventory can be recorded and given proper attention.
Inventory planning can let you search for adjustments with items, item quantity, total supply, final quantity, and whether or not those items are being used by any MRP system.
Support Important Managerial Decision Making
Managers use advanced planning and scheduling solutions to improve their decision-making regarding production demands, production sequences, and predicted changes in production. APS software helps your business react to real-time production efficiency changes or the impact that changes in your scheduling may have on your business.
Examples include machine breakdown or parts being scrapped. Advanced scheduling supports what-if scenarios such as:
- “What is the cost of accepting an urgent order?”
- “Will prioritizing a new urgent order hurt our completion time for other pending orders?”
- “Can we afford to pay our employees overtime to complete this job?”
- “When can we move a machine into a maintenance stage without slowing down production?”
APS software will help you see the true effect of each scenario. Most solutions can provide a dashboard or KPIs to help managers visualize the effect their decisions will have.
Integrate Your Operations With ERP, MES, and Supply Chain Systems
Advanced planning and scheduling systems are a great addition to existing manufacturing software environments. They help aid in managing your manufacturing processes that are usually performed by one or multiple:
A few APS solutions include integration wizards. Other times, an APS software vendor may specialize in integrating their solution with a specific ERP or MES. The biggest benefit of complete integration with other business management systems is having a complete view of your operations.
Businesses want to avoid duplicate entries or data transfers from one system to another whenever they receive new sales orders, hire new workers, or purchase new machines. They want a system that can seamlessly transfer data from the planning and scheduling phase into their ERP solution.
Production Planning with APS Software
Proper production planning will utilize the resource allocation of employees, materials, and capacity to ensure the wants and needs of all customers can be met. A production planning module in APS software aims to determine the required product mix, match the desired production level to existing resources, schedule the work, and create orders for your employees and facilities to follow.
Once orders have been planned, production starts. However, urgent requests or rushes may come through, which can throw a wrench into your original production plan. How will you meet your existing deadlines? How can we avoid the costs involved with late deliveries? How do we schedule new urgent orders with confidence?
Proper production planning with APS software can avoid these headaches by ensuring smooth production order processing, reliable planning and delivery dates, and optimized costs and resource utilization. APS software will let you plan orders based on current production stages while maximizing throughput to ensure all orders are delivered on time.
MRP Improvements with APS Software
Material requirements planning, or MRP software, helps streamline the manufacturing process through production planning, scheduling, and inventory control. Similar to APS software, MRP also aids in inventory and production schedules to produce products and complete manufacturing jobs. An MRP system determines which assemblies must be built, what materials must be purchased, and the order in which to build products to meet customer due dates.
APS software can be thought of as an enhancement to an MRP process. The information that goes into APS software includes your forecast, stock levels, and sales orders. You also need to include your resource capabilities and target stock levels defined by stock-keeping units (SKUs). The output in APS software is an achievable production load for the desired product.
When your forecast for shipments exceeds your capacity, you must change the scheduled production or move it to another area or facility that can meet production within any time constraints. To determine the best movement for your production, you’ll need software that can handle “what if” scenarios, which will let you find the best fit with no capacity issues.
Compared to MRP software, APS software can increase throughput while reducing work in process and raw material inventory.
Production Scheduling vs. Advanced Planning and Scheduling
The most significant difference between production scheduling software and advanced planning and scheduling software is in the name. Both options can provide near-identical functionality but are likely being marketed under different terms by the software providers.
Other synonyms for the software include production planning software and advanced production scheduling software. Some argue that production scheduling is just one of the many features included within APS software, which implies that APS software is (as the name implies) an advanced version of production scheduling software.
However, at their core, both production scheduling software and APS software will be able to upload a number of orders that need to be processed according to specific operations and product routings. Both systems will be able to create a schedule that can be viewed in various ways, but typically as a GANTT chart. These charts will detail how orders will be produced across different processes.
In many cases, the end-user can modify the production schedule and use various “what-if” scenarios to play around with different situations on the production floor. In addition to calculating material consumption, APS systems can prevent the scheduling of production orders after any material has run out, as well as automatically generate supply orders once any material has partially run out.
Pricing Guide
APS software pricing is typically based on deployment model (cloud vs. on-premise), number of users, and the depth of features included. Costs generally scale with system complexity, integration requirements, and the level of real-time scheduling you require.
Entry-Level from $50 to $150 per user/month:
- Basic scheduling and resource management tools with limited automation and no advanced optimization. For example, Visual Planning starts at $55/month for full desktop planners.
Mid-Tier from $500 to $2,000 per month:
- APS modules with finite scheduling, visual dashboards, and basic constraint management, often add-ons to ERP or MES systems. For example, TACTIC (on-premise) falls in this range, dependent on user count.
Large-Scale from $2,000 to $5,000 per month:
- Full-featured APS platforms with dynamic rescheduling, integration with shop floor data, and multi-site coordination.
Enterprise from $5,000+/month + setup fees:
- High-end systems with scenario modeling, AI-driven optimization, and deep ERP/MES integration. Setup and customization may exceed $10,000. For example, Optessa starts around $5,000/month and targets large, global manufacturers.
Most systems also charge implementation fees for configuration, training, and data migration—especially if deep customization or third-party integration is required. Many vendors offer modular pricing, allowing companies to license only the planning or scheduling components they need.