What is a Warehouse Management System?
A warehouse management system is a software application that coordinates inventory and warehousing operations throughout distribution centers. Often shortened to WMS, these systems offer various functionalities for greater control over typical warehouse operations.
Features and Benefits
Feature | Description | Benefit |
---|---|---|
Inventory Tracking | Enables real-time tracking of stock levels and locations within warehouses using unique identifiers like SKUs, barcodes, or RFID tags. | Helps prevent stockouts and overstocking, maintaining optimal inventory levels. |
Order Management | Automates the order processing workflow, from order receipt to fulfillment and shipment. | Improves delivery times and customer satisfaction, as orders are fulfilled accurately. |
Picking Optimization | Leverages various picking methods, such as batch, wave, or zone picking, to efficiently collect items for orders. | Boosts picking efficiency, reduces labor costs, and shortens order cycle times. |
Barcode and RFID Scanning | Supports RFID and barcode scanning for more accurate tracking of inventory during receiving, picking, and shipping. | Results in more accurate inventory management, reducing human error and improving operational efficiency. |
Shipping Management | Integrates with shipping carriers to manage activities like label generation, tracking, and cost calculations. | Streamlines shipping processes, which can reduce costs and improve delivery times. |
Slotting Optimization | Analyzes inventory movement and product demand to determine the best placement of items within the warehouse. | Optimizes product placement and reduces travel time for pickers, enhancing efficiency and speeding up order fulfillment. |
Return Management | Facilitates the processing of returned items, including logging returns, inspecting items, and restocking as needed. | Streamlines return processes to improve customer satisfaction by enabling quick handling of returns and minimizing disruption to inventory. |
Looking for warehouse management software? Request free software recommendations from one of our advisors now.
Types of Warehouse Management Systems
Standalone WMS
Basic systems focused solely on warehouse management functionalities like inventory control, order management, and picking and packing processes.
- Best For: Small to mid-sized warehouses looking to upgrade from manual tracking systems or spreadsheets.
- Example: Zoho Inventory
ERP-Integrated WMS
Modules within broader ERP systems with advanced inventory and warehouse management tools alongside functionalities like finance, HR, and supply chain management.
- Best For: Larger businesses that want an all-in-one solution instead of several separate systems.
- Example: NetSuite
Supply Chain Execution System
Software with basic logistic operations alongside transportation management, warehousing, and other supply chain operations.
- Best For: Enterprises needing end-to-end supply chain visibility and control.
- Example: Oracle SCM Cloud
Cloud-Based WMS
Systems that are run in a hosted environment accessible through web browsers; are often provided as SaaS (Software-as-a-Service) solutions.
- Best For: Businesses seeking flexibility, scalability, and lower upfront costs.
- Example: Fishbowl Inventory
On-Premises WMS
Systems deployed locally on company servers and managed by in-house IT teams.
- Best For: Companies with strict data security needs or those requiring full customization.
- Example: NorthStar WMS
Open-Source WMS
Software with basic warehouse management features and customizable source code.
- Best For: Small businesses with technical expertise that want a low-cost customizable option.
- Example: Odoo
Common Questions about Warehouse Management
Here are some frequently asked questions about warehouse management systems and practices:
How do warehouse management systems optimize operations?
The first way WMS optimizes warehouse operations is through organizing processes into a centrally controlled system. For instance, digitizing inventory records by scanning barcodes can reduce the amount of paperwork your warehouse would otherwise need to process with every inbound shipment and outgoing delivery.
Additionally, warehouse management organizes and optimizes storage space. An analysis of the existing layout can reveal areas for improvement, such as pairing frequently purchased products together or placing items from the same product line in specific zones for easier retrieval. Pickers can then check the computer-based WMS to determine where any piece of merchandise is located throughout the warehouse in real time, all without having to waste time physically checking storage units themselves.
How does warehouse management improve order picking?
Order picking refers to the selection of merchandise selected from storage to fulfill specific purchase orders. A well-constructed warehouse management system can use multiple picking and fulfillment methods to optimize product distribution. Primary methods include:
- Batch picking
- Cluster picking
- Discrete order picking
- Wave picking
- Zone picking
After using a WMS to organize a warehouse’s layout, order picking can be streamlined as well through more efficient picking paths. Changing up or combining picking methods, such as discrete or batch picking, can further improve operational efficiency. All of these factors make a major difference when it comes to customer satisfaction, as more efficient picking means faster fulfillment and deliveries. There is also warehouse order picking software to help optimize order selection.
How does WMS improve employee productivity and satisfaction?
Increasing order-picking efficiency means warehouse employees have an easier workload. No more making multiple trips to fulfill orders, and no more wasted time manually checking every order for accuracy before shipping. Automation of fulfillment processes lets them instead focus their time on other important tasks, making the warehouse more productive than ever before.
How does warehouse management differ from control and execution systems?
Over the years, a lot of different systems have been designed to streamline distribution center operations. Warehouse control and warehouse execution systems, shorted to WCS or WES, are just two examples. The first, execution, provides vital logistics for on-site operations. Control is more focused on real-time operations within the warehouse or distribution center. All of these solutions are capable of being integrated together to provide a complete warehouse operating system.
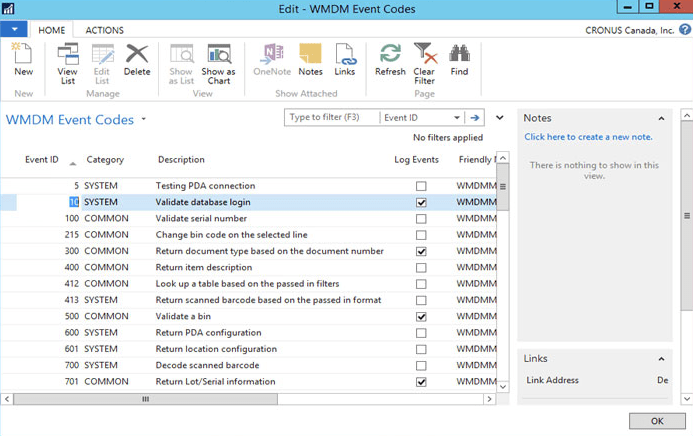
How is a WMS different from inventory management systems?
As described, warehouse management systems provide an overview of all warehouse operations, including the inventory stored within. Inventory management or control software tracks all information about the items your company builds, buys, stores, transports, or sells, regardless of whether they pass through a warehouse or distribution center. The WMS is more about coordinating logistics from inbound and outbound transportation, employee scheduling, and measuring performance analytics.
Additionally, inventory management in a warehouse setting helps differentiate between product batches. Merchandise can be tracked from pallets down to individual units. This advanced inventory control allows warehouse managers to break up larger units into smaller packs to fulfill individual orders as needed.
How do WMS coordinate with transportation management?
As one part of supply chain management, WMS ties in closely with the transportation and delivery of merchandise to vendors, retailers, and customers. Transportation management (TMS) or trucking software automates this aspect of the supply chain, though it must coordinate with warehouse management systems to ensure timely deliveries and shipments. Without an established WMS, cross-docking is impossible as inbound and outbound shipments may be delayed from reaching their final destination.
Food and beverage distributors, in particular, need to work closely with transportation or trucking logistics to prevent spoilage during delivery. eCommerce businesses which ship products directly to customers will also want to ensure clear communication with transportation services to improve customer satisfaction.
How do warehouse management systems work with third-party logistics?
Many warehouses have to work with third-parties at various points along the supply chain. There are integrated management systems for third party warehouses (3PL warehouses) that are not directly controlled by your company but impact your supply chain. For example, a third-party manufacturer may not know a warehouse is at capacity, thus causing overstock with their next delivery. Coordinating 3PL with your WMS can prevent these issues before they happen.
Further reading: Discover the best 3PL software.
Automate Warehouse Management with Software
Implementing warehouse management software (WMS) is one of the many ways to automate your complex warehouse operations. With software, warehouse managers can review inventory levels, labor schedules, and 3PL deliveries all from one source. This modern approach to warehouse optimization streamlines order fulfillment more than ever before.
Operating as standalone systems or as part of a larger enterprise resource planning (ERP) package, these solutions allow managers and laborers to automate everything happening on the warehouse floor. Cloud-based WMS makes inventory data accessible from anywhere, perfect for multi-warehouse operations. On-premise implementation allows for coordination between hardware and software.
Finally, the functionality of your warehouse management system directly ties into customer satisfaction. Using WMS can improve your customer relationship management (CRM) by keeping orders accurate and delivered on time.