The Best Construction Project Management Software
Construction project management software can help you plan, manage, and execute projects efficiently. We tested and ranked the top systems for general contractors, specialty trades, and home builders.
- Allows photo uploads to show project progress
- Encourages collaboration between users and contractors
- Responsive technical support team
- 100 day money back guarantee
- Integrates with 50+ other systems
- Residential and commercial
- Automates emails, document sharing, and photo archiving
- Customizable reporting
- Integration with AutoCAD and Revit
Whether you’re just getting started in construction or you’ve been managing projects for many years, find solutions that streamline estimating and bidding, project scheduling, field management, and integrated job costing.
Feature Comparison
Construction Management Software | Project Management | Budget & Cost Tracking | Document Management | Bid Management |
---|---|---|---|---|
Contractor Foreman | ✅ | ✅ | ✅ | 🟡 |
Buildertrend | ✅ | ✅ | ✅ | ✅ |
Houzz Pro | ✅ | 🟡 | 🟡 | ❌ |
Procore | ✅ | ✅ | ✅ | ✅ |
Jonas Premier | ✅ | ✅ | ✅ | ✅ |
CHS | 🟡 | ✅ | ✅ | ❌ |
Projul | ✅ | 🟡 | 🟡 | ❌ |
Viewpoint Team | ✅ | ✅ | ✅ | 🟡 |
HCSS HeavyJob | 🟡 | 🟡 | ✅ | ❌ |
123worx | ✅ | 🟡 | 🟡 | 🟡 |
InEight | ✅ | ✅ | ✅ | ✅ |
JobPlanner | ✅ | ✅ | ✅ | ✅ |
Legend:
- ✅ = Fully Featured: The software supports this feature and offers advanced capabilities (i.e. project scheduling with full Gantt chart functionality and dynamic task dependencies)
- 🟡 = Basic Features: The software offers minimal support for this feature, covering only essential functions. (i.e. project scheduling with simple calendar views and basic task assignments)
- ❌ = Feature not supported
- Autodesk: Best Building Information Modeling (BIM) Integration
- Contractor Foreman: Best for Residential Contractors
- Procore: Best for General Contractors
- Buildertrend: Best for Home Builders
- Houzz Pro: Best for Renovations and Remodels
- Viewpoint Team: Best for Commercial Contractors
- JobPlanner: Best Value Option
- Fieldwire: Best Free Plan
Autodesk - Best Building Information Modeling (BIM) Integration
Autodesk Build’s BIM integration can enhance project coordination and improve your decision-making, helping minimize errors and streamline your construction workflows. In the pre-construction phase, you’ll need to collaborate with architects and engineers to develop a 3D BIM model using tools like Revit or AutoCAD. This foundational model allows you to integrate advanced features throughout the project lifecycle.
For example, the system’s quantity takeoff capabilities can generate accurate material lists directly from the model, allowing for precise procurement planning. Additionally, a 4D simulation can link your construction timeline to the model so you can visualize the sequence of activities and optimize resource allocation.
Your on-site teams can then use their tablets to access the BIM model, which ensures that everyone has the latest version and eliminates the need for paper plans. Any field dates, such as modifications to electrical wiring, can automatically be logged in the model and shared with your team. You can then provide your client with the final model that includes all detailed documentation for facilities management and future renovations.
This construction manager software best serves contractors already using other Autodesk products like Autodesk Docs and BIM Collaborate. It starts at $165/user/month or $1,625/user/year with the annual billing discount. Smaller companies may struggle to justify the investment, especially if they’re not already in the Autodesk ecosystem.
Learn more about Autodesk Build features and pricing.
Contractor Foreman - Best for Residential Contractors
Contractor Foreman helps contractors keep clients informed and up to date on each job’s progress with a dedicated client portal. This is especially important for residential contractors with clients eager to stay informed about each project step. Contractor Foreman is also affordable at $49/user/month; however, it does not include the client portal out of the box. This requires users to go with the Pro plan, which costs $166/month.
The client portal lets contractors fully customize the information shared, tailoring it to each client’s needs and preferences. This ensures that sensitive or non-essential details remain secure and private. This saves you time by cutting down on client communication, allowing you to focus on overseeing projects. The portal includes the following capabilities:
- Estimates: Let clients approve or deny estimates directly from the portal.
- Change orders: Let clients suggest or submit project changes and receive updated pricing when those changes are made.
- Project updates: Provide updates to clients when you hit specific milestones, such as completion of flooring installation, electrical work, or inspections.
- Project documents: Upload pictures or files of the job site so clients can view daily progress or review previous plans or proposals.
- Invoices: Let clients pay for completed work directly from the portal, simplifying the billing process.
The dedicated messaging module archives and stores client communications, helping contractors deliver effective customer service while documenting every exchange. If disputes or issues arise, this construction PM software provides a clear record of interactions, building trust and transparency.
Read our full Contractor Foreman review.
Procore - Best for General Contractors
Procore simplifies bid management, for general contractors struggling with multiple subcontractor bids. Along with its full project management suite, this construction software lets you quickly organize and select the most competitive bids.
You can create bid packages by entering general information like bid number, due date, bidding instructions, and project overview, with the option to save these as templates for efficiency. You can also attach and update drawings, documents, and job specifications when changes occur, ensuring the bid reflects the latest details.
From there, select and filter subcontractors by location, trade, pre-qualification, or type, such as small, women-owned, or minority-owned businesses. Once finalized, Procore sends the bid packages to the selected subs, letting you track views, document access, and recent updates.
Buildertrend is another popular choice for general contractors, known for its user-friendly interface and streamlined bid request and proposal management. However, it lacks the sophisticated tracking and analytics tools Procore offers, making Procore better suited for general contractors handling multiple larger, more complex projects. Procore’s strength lies in its ability to manage multi-phase bids and its automation features. Its pricing starts at $375/month though final costs depend on your annual construction volume (ACV), which can be a drawback for smaller contractors.
For general contractors looking for a more standardized pricing model, we recommend comparable options such as 123Worx.
Read our full Procore review.
Buildertrend - Best for Home Builders
Buildertrend offers a dedicated module that streamlines warranty claims management for home builders, protecting your company’s reputation. A structured process not only improves client satisfaction but also boosts referrals and repeat business, setting great builders apart from the rest.
With Buildertrend, you can easily store all warranty documentation for each home, including manufacturer warranties and your builder’s own coverage for workmanship, structural defects, and major systems like HVAC, plumbing, and electrical.
According to WarrantyWeek, D.R. Horton, the country’s largest home builder, saw a 25% increase in warranty claims in 2022. Buildertrend simplifies the process for both homeowners and contractors. Homeowners can easily log into their portal and submit claims by detailing the issue, setting priorities, and uploading supporting documents. You’ll receive these claims automatically, enabling quick follow-up.
From there, you can assign a team member or trade partner to address the issue. The contractor who performed the work is notified, and if approved, you can schedule a service appointment or allow the contractor to coordinate directly with the homeowner.
After resolving the claim, homeowners can leave feedback, helping to build trust and secure future referrals and positive reviews. Buildertrend starts at $499/month, making it a solid choice for small to mid-sized construction companies with 10-50 employees and annual revenues between $1 million and $15 million.
Read our full Buildertrend review.
Houzz Pro - Best for Renovations and Remodels
Houzz Pro equips contractors with tools to source new clients and deliver impressive models of their remodeled spaces. The 3D visualization tool lets you scan a room with any mobile device, creating an accurate floor plan and 3D model. Once the scan is complete, you can work with clients to add cabinets, windows, fixtures, and even furniture, visually showcasing the finished project. Entire walls can be moved or kitchen islands added, enabling homeowners to explore all their renovation options.
To add more precision to these 3D visualizations, Houzz Pro partners with industry leaders like Sherwin-Williams and Kohler, providing exact product details and measurements for items the client selects. Even if a brand isn’t partnered, contractors can easily pull product pricing data from suppliers’ websites or their own price books, speeding up the quoting and design process.
Houzz Pro’s Essentials plan for designers starts at $149/month, including the 3D planner tool. With competing bids forcing prices to the ground, having a tool like Houzz Pro allows you to build trust with homeowners, decrease the time it takes to quote projects, and leverage new technology to win more jobs.
Read our full Houzz Pro review.
Viewpoint Team - Best for Commercial Contractors
The Viewpoint Team mobile app provides a clear communication channel for internal and external teams, including superintendents, project managers, subcontractors, and project engineers. When inevitable changes or delays occur on a large commercial job, everyone involved can quickly reference Viewpoint Team to check the next steps. This keeps your costs low and the job on schedule.
For example, consider a scenario where glass panels arrive damaged late in the day. Usually, the project manager or foreman has to call the superintendent to the job site and coordinate with the supplier for a new shipment, which could take days to resolve. Using the Viewpoint Team mobile app, field workers can quickly take a picture of the damage, submit an issue report, and automatically have it notify the required parties.
Because Viewpoint Team centralizes all project communication and has an audit trail, it tracks information from start to finish. The mobile app also works offline, enabling contractors to capture and sync data when they regain connectivity, even in areas with limited access.
Viewpoint Team is offered as standalone software for construction companies. However, it’s also natively included within the Viewpoint Spectrum and Viewpoint One construction management systems. It’s best-suited for mid-size to large commercial contractors with 50 to over 1,000 employees, supporting subcontractor management, complex projects, and team coordination across job sites.
JobPlanner - Best Value Option
JobPlanner is a solid construction management software for general contractors, specialty contractors, and homeowners looking for a budget-friendly way to manage construction projects. The job planner tool handles the essentials like bid management, budgeting, invoicing, and change order tracking. Plus, it integrates with leading accounting software such as QuickBooks or Sage, so you can keep your existing accounting systems.
JobPlanner lets you add features as your business grows, with flexible pricing starting at just $25/user/month. However, JobPlanner does not include built-in estimating, so users may need a separate tool for that. But if you’re primarily looking to streamline project management and accounting, this building industry software still delivers strong value for its features.
Read our full JobPlanner review.
Fieldwire - Best Free Plan
Fieldwire offers free construction management software for up to five users and three projects simultaneously. The task engine gives small crews everything they need to coordinate work and record progress, right from their phones.
You can start a task manually or drop a pin on a drawing; each pin stores its X-Y location, CSI category, and an optional location tag, like floor, room, or elevation. From there, you can choose the status (P1-P3 priority), assignee, watchers, start and end dates, and checklist templates. This makes it easier for your team to sort and filter without digging through email chains.
You can snap photos, record videos, attach PDFs, or drop voice-to-text notes to prove progress. Even in remote areas, content syncs the moment you’re somewhere where a connection is available again. Fieldwire notifies assignees and watchers of any changes instantly, and overdue tasks surface automatically in mobile and web views. This can help you spot bottlenecks before they derail your schedule, even for crews with no dedicated PM.
Overall, the free plan is a solid fit if you’re just starting out. However, for tools like RFIs, submittals, change orders, and budgeting, you’ll need the Business Plus plan at $89/user/month.
Learn more about Fieldwire’s subscription plans on our review page.
Systems We Don’t Recommend
- Monday.com: While Monday.com does offer a system for managing simple projects and tasks, it requires extensive customization to meet the needs of construction management companies.
- Zoho Projects: Construction projects often require specialized features like BIM integration and cost estimation tools, which Zoho Projects doesn’t natively support.
- Wrike: The system is a versatile project management software, but it lacks specialized features like RFIs and submittals and field-specific functionalities like mobile field apps.
What is Construction Management Software?
Construction management software is a set of tools that help construction companies and contractors manage their projects from start to finish. These platforms provide capabilities for project scheduling, job costing, budgeting, bid management, and client communication.
Each contractor or company has its own way of managing jobs, so figuring out which software fits your workflow is crucial when adopting software for construction management. Below is a list of common construction industries and what they do.
-
General Contractors: They manage the entire construction project, from overseeing subcontractors to procuring materials and scheduling projects. GCs ensure the project meets the required specs and stays on budget from start to finish.
-
Home Builders: Home builders specialize in constructing new residential buildings ranging from custom homes to entire neighborhoods. Like GCs, they manage the material, permits, and subcontractors from start to finish.
-
Specialty Trade Contractors: These contractors focus on specific trades within construction. Some examples include plumbing, electrical, HVAC, or framing. They’re hired because of their specialized knowledge of their trade.
-
Renovation/Remodeling Contractors: These contractors work to improve or refresh existing structures, such as kitchen remodels, home additions, or office updates. They can work on both commercial and residential projects, but they typically handle the entire project themselves.
-
Residential Contractors: Residential contractors specialize in new townhouses, condos, and apartment complexes. They manage projects from site prep to final inspections.
-
Commercial Contractors: Commercial contractors manage projects for buildings such as offices, retail spaces, hotels, or warehouses. They must ensure that buildings meet commercial codes and standards.
-
Civil Contractors: These contractors focus on roads, bridges, and tunnels. They specialize in earthworks site prep and typically do smaller infrastructure projects.
-
Large Infrastructure Contractors: Infrastructure contractors focus on extensive infrastructure projects, including large transportation systems like railroads, highways, utilities, and energy projects.
-
Construction Consultants: Consultants provide expertise and advising services for construction projects. They can manage specific tasks or the entire project. Services range from planning to estimating to ensuring compliance.
Common Challenges
Here are the most common challenges that construction management software is designed to solve:
- Project Delays: Tight deadlines with unforeseen delays can disrupt timelines, damage client relationships, and increase costs.
- Budget Overruns: Unexpected costs from poor planning or inefficient resource allocation, coupled with the increased fluctuation of material costs, can lead to budget overruns. This can hurt the bottom line and put a project in the red.
- Workplace Safety: Accidents can cause significant delays or even lead to legal troubles. Maintaining high safety standards is a crucial challenge for the construction industry.
- Communication Gaps: If project details or job site issues are not communicated promptly, miscommunication between teams, contractors, and other stakeholders can lead to costly errors.
- Regulatory Compliance: Staying current with local, state, and federal regulations can be time-consuming and difficult. Furthermore, non-compliance can lead to cost penalties and a loss of clients’ confidence.
- Document Control: Tracking estimates, change orders, project plans, or other documents can be overwhelming for small and large projects, especially for contractors still using paper methods.
- Skilled Labor Shortage: With an ever-shrinking population of skilled labor, construction companies must maximize the productivity of their existing workers.
- Resource Management: Poor equipment, labor, and materials allocation can lead to slow project progress, increased costs, and dissatisfied customers.
Core Features
Construction project planning software includes these key capabilities:
-
Bid Management: Simplifies creating bid packages, tracking bids, and generating professional proposals or estimates. Bid management tools can help automate routine tasks and organize bid packages.
-
Change Order Management: Automates creating, tracking, and approving change orders, preventing delays and ensuring transparency. It also ensures that all stakeholders and clients are informed of any project changes.
-
Daily Field Reports: Allows teams to input daily hours, job photos, and project updates from the site to ensure everyone is on the same page.
-
Subcontractor management: Helps schedule subcontractors, track performance, manage communication, and ensure subcontractors are insured and compliant.
-
Quality and Safety Compliance: Manages and schedules safety inspections, stores compliance documentation, and tracks incident reports. It automates the process of on-site reports and helps reduce the risk of accidents.
-
Client Communication: Improves transparency with client portals to update project progress, schedules, and documentation. This can also ensure clients approve and sign off on all change orders, further building trust.
-
Job Costing: Tracks and categorizes project costs into labor, material, or equipment. This can be further broken down by individual jobs, suppliers, or any other granular report that helps understand the outflow of costs.
-
Scheduling Management: Provides a real-time view of ongoing project timelines. Helps predict where projects could get bottlenecked and provides notifications or alerts when key tasks are due or completed.
Is it Time to Ditch Pen and Paper?
Based on a recent technology survey by Software Connect, here are some of the top trends for buyers looking to purchase construction software:
80% of all companies looking for software rely on manual methods to carry out basic business functions. If you struggle to make Excel spreadsheets or even pen/paper methods work, it may be time to get up to speed.
Over 70% of contractors are looking for job costing and project tracking functionalities, with about 67% of respondents also requiring estimating capabilities. While this does not dictate what your business needs, it does provide some guidance on what other companies are doing.
56% of construction businesses are currently not using construction management software. With that number growing yearly, it’s important not to be left behind.
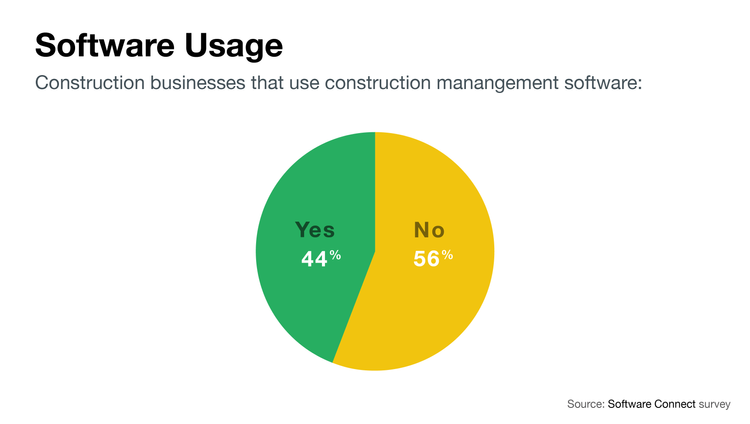
What’s Best for My Construction Company?
Choosing the right construction software will depend on the type of projects you work on. This table matches recommended platforms with the type of construction services offered to help you identify the best solution for your company.
Contractor Type | Recommended Systems | Key Features | Type of Projects |
---|---|---|---|
Residential Construction | Contractor Foreman, Buildertrend, Houzz Pro | Scheduling management, client portals, 3D floor plans | Single-family homes, residential renovations |
General Contractors | Procore, Jonas Premier, Contractor Foreman | Bid management, client portals, collaboration tools | Office buildings, shopping malls, hotels |
Home Builders | Buildertrend, Procore, CHS | Scheduling management, budget tracking, 3D floor plans | Custom homes, residential complexes |
Specialty Trade Contractors | Projul, Contractor Foreman, Procore | Crew scheduling, job costing, daily field reports | Plumbing, electrical, HVAC installations |
Renovation and Remodeling Contractors | Houzz Pro, Buildertrend, Projul | 3D floor plans, selections, client communication | Home remodels, interior renovations |
Commercial Contractors | Viewpoint Team, Procore, 123worx | Collaboration tools for subs, project management | High-rise buildings, industrial parks, retail buildings |
Civil Contractors | HCSS HeavyJob, InEight, Viewpoint Team | Daily job/equipment tracking, environmental impact | Highways, bridges, large-scale infrastructure |
Still not sure what’s best? Talk to one of our software advisors for free customized help.
Pricing
One of the key factors when looking into construction management software is its pricing. These software platforms vary heavily based on which features are included, the number of users, or even the amount and size of projects you work on at one time.
For example, Contractor Foreman starts at $49/month for one user and includes 35 basic features. Alternatively, another popular system, Procore , starts at $375/month for small-volume builders. Larger contractors typically charge based on the organization’s ACV.
-
Entry-Level Solutions: Range from $5,000-$15,000 per year
-
Mid-Market Software: Range from $15,000 to $50,000 per year
-
High-End Systems: Range from $50,000 to $150,000 per year
-
Enterprise-Level Software: Over $150,000 per year
-
Software as a Service (SaaS): Cloud construction software offers pricing as a monthly or annual subscription that you pay over time. Cloud system subscriptions can start at around $25/user/month and can increase to well over $1,500/month for larger contractors. Additionally, setup and training fees can cost between $500 to $20,000 depending on the complexity or customization required to implement.
-
On-Premise Software: Also known as locally installed software, on-premise software generally requires a significant initial investment to get started. These solutions tend to start at around $10,000 to $50,000. This investment will cover licensing fees, setup fees, and training costs. On-premise solutions are typically only for contractors with an established IT infrastructure or those comfortable paying for ongoing support ranging from $1,000 to $20,000 annually.
Understanding what other small and medium contractors spend on software might help you determine your own budget. Over the past few years, we surveyed hundreds of construction companies across all industries. Our findings showed that most companies spend about 1-2% of their annual revenue on software expenses, as referenced in the graph below.
To calculate your software spending, multiply your annual revenue by .015 to get a rough idea of what you should expect to spend.
Trial Periods and Free Plans
Some solutions offer trial periods or a free plan, enabling you to test the software before purchasing. Out of our product picks, Contractor Foreman, Houzz Pro, and JobPlanner offer free 30-day trials.
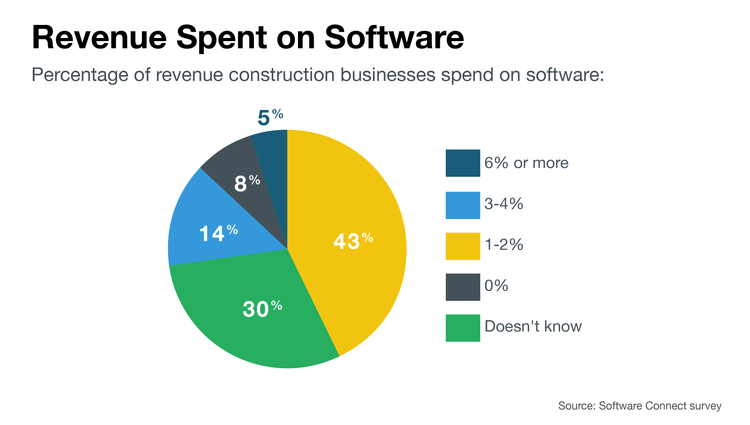
Frequently Asked Questions
What are the key features I should look for in construction management software?
How do I choose the right construction management software for my business?
Choosing the correct software will depend on your project size, type of construction (residential, commercial, civil), specific features, and budget.
We can help provide suggestions for your construction business. Talk to one of our free advisors
What are the typical implementation timelines for construction management software?
Does construction management software scale as we grow our business?
Many construction management platforms offer scalability, allowing you to add users and features and your company or project expands. However, some programs are truly made for smaller contractors while other systems are specifically for larger well established firms.
We can recommend systems that best suit your business for today and plan ahead for tomorrow.