The Best Furniture Manufacturing Software
In this guide, we analyzed solutions handling multi-part assemblies and tracking diverse materials. Here’s our list of the top furniture ERP software, factoring in features like real-time inventory control and financial management.
- Free trial available
- New eCommerce additions
- Low total cost of ownership
- Integration with AI, MI, IoT, and cloud-hosting
- Offers hybrid on-prem and cloud platform
- Over 40 years of manufacturer and distributor expertise
- Affordable, transparent pricing
- Responsive live support
- Real-time inventory tracking across locations
We evaluated the top furniture manufacturing software using our advanced review methodology. Here’s a rundown of the best products based on pricing, scalability, whether they can handle multi-level bill of materials (BOMs), and key features like supply chain management and production planning.
- xTuple: Best Overall
- SYSPRO: Best for Diverse Product Lines
- Katana MRP: Best for Production Planning
- MRPeasy: Best BOM Management Tools
- Epicor Kinetic: Advanced Inventory Management
- JobBOSS²: Best for Custom Job Shops
- Infor CloudSuite Industrial: Most Scalable Solution
- Deskera ERP: Strong Financial Management
xTuple - Best Overall
xTuple’s work order management system makes it easier to juggle custom orders and repeatable designs. Whether you’re manufacturing a one-of-a-kind dining set or a popular furniture piece, you can input all production details needed to complete the job. For recurring models, xTuple automatically fills in your BOM and routing steps through your pre-configured product records. For custom creations, you can manually enter specific materials and processes to ensure accurate tracking for every project.
If your business works with multi-part furniture like sectional sofas, xTuple can help you track all components. This might include different types of wood, finishes, and hardware. This helps you keep on top of material costs and availability before production ever starts so you can better control budgets and timelines.
Routing is equally straightforward. You can assign tasks like sanding, cutting, or staining to specific workstations. As you complete each step, the system updates your inventory so you always know how many materials you’ve used. Plus, xTuple provides travelers that move with each project. These easy-to-read documents include all manufacturing guidelines, along with barcodes for quick tracking.
Because it offers a flexible approach to user licensing, xTuple is ideal for startups and small businesses with smaller teams. Pricing starts at around $175 per user per month, with plans based on the number of named users actively accessing the software. For the manufacturing edition, there’s a five-user minimum.
While budget-friendly, xTuple’s workflows can sometimes feel rigid. Features like unlabeled toolbar icons can add to the initial learning curve, but you can find plenty of training videos on the official YouTube channel. Additionally, xTuple’s Basic Training or EssentialsPlus plan includes extra post-onboarding support.
For ratings and pricing details, see our full xTuple review.
SYSPRO - Best for Diverse Product Lines
For furniture manufacturers dealing with diverse product lines, SYSPRO handles both simple and complex BOMs. It allows you to account for various design elements, material variations, and production processes seamlessly.
Its version control system is crucial in maintaining product consistency and quality. It allows for transparent BOM revisions, ensuring that any changes are well-documented and tracked. This level of traceability is essential in the furniture industry, where product variations and customization are common.
Katana MRP - Best for Production Planning
Katana MRP delivers real-time insights into your furniture production process, design changes, and raw material consumption. For furniture manufacturers looking to move away from static spreadsheets, Katana offers a dynamic solution. Its BOM module automatically allocates available raw materials and products, ensuring efficient resource allocation and schedule prioritization.
You can easily adjust raw material and resource costs by tracking sales and production orders in real-time, simplifying pricing decisions. Multi-level BOMs with subassemblies further enhance cost analysis, providing a clear understanding of product margins and the cost of goods sold.
MRPeasy - Best BOM Management Tools
MRPeasy features a versatile and tailored approach to managing the bill of materials (BOM). It offers the flexibility to handle both single-level and multi-level BOMs, making it adaptable for small to mid-sized furniture businesses.
MRPeasy doesn’t treat BOMs in isolation but integrates them seamlessly with production planning, purchasing, and sales. This comprehensive approach makes MRPEasy a good choice as a complete MRP software solution for furniture manufacturers. The built-in version control system ensures easy and transparent BOM revisions, enhancing traceability in the production process.
Epicor Kinetic - Advanced Inventory Management
Epicor Kinetic offers real-time visibility into inventory levels, allowing furniture manufacturers to manage raw materials and finished goods. This feature allows furniture manufacturers to monitor stock levels accurately, reducing the risk of overstocking or running out of critical materials. The platform also allows for precise control over inventory costs. Furniture manufacturers can track the cost of materials, monitor cost fluctuations, and adjust pricing accordingly, optimizing profit margins.
Epicor Kinetic’s inventory management tools also extend to resource allocation, ensuring that materials are allocated efficiently to production orders. This minimizes waste and maximizes the utilization of resources, such as machinery and labor.
JobBOSS² - Best for Custom Job Shops
JobBOSS² is well suited for make-to-order job shops because of its strong estimate and quoting module. It helps ensure estimates are accurate for unique or semi-custom pieces, which vary in materials, finishes, and hardware. You can easily look up the parts in the search bar and edit the cost or price if something is completely custom. The system also gives you exact job margins, eliminating manual calculations and errors.
Once you complete the estimate, you can seamlessly transfer all the information to make the customer quoting process more efficient. With just a few clicks in the item editor, you can further adjust quantities and costs so your clients receive accurate, concrete quotes. You can also fill in exact customizations, such as different types of wood, specific dimensions, or even custom embossing. From there, you can email the finished quote from the same screen, streamlining the process.
JobBOSS² is made specifically for small manufacturers with 1-50 employees. It’s a great option if you’re just upgrading from QuickBooks and need something more advanced. Pricing starts at $3,000/year, but you’ll need a custom quote for exact costs. If you’re a larger operation, a system like SYSPRO or Epicor Kinetic may be a better fit.
Infor CloudSuite Industrial - Most Scalable Solution
Infor CloudSuite Industrial is highly scalable because it is built on a modular architecture. This allows businesses to select and implement only the modules that suit their needs. This modular approach means that smaller businesses can start with essential functionalities and expand their software capabilities as they grow.
For larger furniture manufacturers or businesses with multiple locations, Infor CloudSuite Industrial offers multi-site support. This feature ensures that the software can handle the complexities of a larger operation while maintaining centralized control and visibility.
Deskera ERP - Strong Financial Management
Deskera ERP integrates financial management with manufacturing operations. This integration allows furniture manufacturers to monitor costs, track expenses, and optimize resource allocation in real time. Financial planning becomes a central component of maintaining quality and profitability.
Its advanced quality control features align with financial planning by reducing the cost of quality-related issues. By implementing rigorous quality control processes and standards, furniture manufacturers can prevent costly defects, rework, and customer dissatisfaction.
What is Furniture Manufacturing Software?
Furniture manufacturing software helps businesses optimize lead times, meet customer demand, and increase profitability through efficient inventory control, supply chain management, production planning, and quality control. This industry-specific type of manufacturing ERP platform addresses the unique offerings and production quirks of the furniture business.
End-product and made-to-order furniture manufacturers using software can automatically manage the entire manufacturing process, from obtaining raw materials to assembling the final product. And assembly-based furniture providers can use the same tools to ensure the correct parts kits, instructions, and sub-assemblies are in the same package. The software also tracks sales orders, plans production schedules, and creates accurate estimates for custom products.
Many solutions tailored to the furniture manufacturing industry are really full enterprise resource planning (ERP) tools. These solutions include modules for manufacturing processes and other business processes like human resources, payroll, and customer relationship management.
Choosing the Best Software
1 Assess Material Planning and Inventory Management Capabilities
- Material Optimization: Evaluate the software’s ability to optimize material usage, minimize waste, and accommodate different materials used in furniture production (e.g., wood, upholstery).
- Inventory Control: Assess the software’s features for maintaining optimal stock levels, preventing overstocking or stockouts, and managing inventory efficiently.
2 Examine Customization and BOM Management
- Customizable BOM: Ensure the software supports highly customizable Bill of Materials (BOM) management, enabling you to create and revise BOMs precisely to meet the unique requirements of various furniture product lines.
- Multi-Level BOMs: Confirm that the software can handle multi-level BOMs with ease, especially if your furniture manufacturing involves complex assemblies or subassemblies.
3 Evaluate Production Scheduling and Resource Allocation
- Production Scheduling: Examine the software’s production scheduling capabilities, focusing on its ability to create detailed schedules considering different product lines, manufacturing processes, and lead times.
- Resource Optimization: Ensure the software allows for efficient resource allocation, such as machinery and labor, to maximize production efficiency and minimize costs.
4 Integrate Financial Management
- Financial Integration: Assess whether the software seamlessly integrates financial management with manufacturing operations. This includes tracking costs, monitoring profitability, and making informed financial decisions in real-time.
- Cost Control: Evaluate the software’s features for cost control and reduction without compromising product quality or consistency.
5 Emphasize Quality Control and Compliance
- Quality Assurance: Examine the software’s quality control features to maintain high product standards. Ensure it helps prevent defects, rework, and customer dissatisfaction through rigorous quality processes.
- Compliance: Check if the software assists in complying with industry regulations and standards, ensuring that products meet safety and quality requirements.
6 Consider Scalability and Growth Support
Scalability: Assess whether the software is scalable to accommodate your business’s growth. It should adapt to the evolving needs of your furniture manufacturing operation, whether you’re a small workshop or a large-scale factory. Modular Architecture: Look for software with a modular architecture that allows you to select and implement only the modules you need, providing flexibility as your business expands.
Key Features
Feature | Functionality |
---|---|
Manufacturing Inventory Management | Track quantities of raw materials, assembly parts, and finished products currently on hand. Automate purchase order processing when supplies run low. |
Quality Control | Lower production costs by using corrective actions to reduce defects in finished products and ensure furniture pieces meet your quality standards. |
Supply Chain Management | Track the flow of goods from acquiring the raw materials to delivering the final product. |
Sales Order Management | Convert sales orders to begin the order fulfillment process, then create corresponding invoices. |
Production Planning | Determine and schedule the materials and labor needed for each manufacturing job to be finished on time. |
Warehouse Management | Keep accurate, real-time records of stock levels in your warehouse storage to know which products are always available. |
Bill of Material (BOM) | Create instructions for furniture assembly and lists of materials, equipment, and hardware needed. |
Benefits
Furniture manufacturers have thousands of product variations to manage at any given time, from fully assembled pieces to individual spare parts. An automated system will track your finished inventory and raw materials like wood, metals, and fabrics. This lets you see what you have available and which product variations can be made with on-hand materials. Many furniture manufacturing systems also include a product configurator module to create a custom piece with a particular size, pattern, color, or material.
Prices of wood, metals, and other raw materials fluctuate frequently–furniture manufacturing software will track these costs in real-time, so you can adjust prices accordingly. And when supplies run low, the software can automatically send purchase orders to prevent production from slowing down.
Pricing Guide
Pricing for furniture manufacturing software depends on your company size, required users, and desired features. Here’s a breakdown of the average cost based on different tiers:
Tier | Size | Average Cost | Examples |
---|---|---|---|
Entry-Level Tier | 1–20 employees | $2,500–$8,000 | JobBOSS², Katana, MRPeasy, xTuple |
Mid-Tier | 20–100 employees | $10,000–$35,000 | MISys Manufacturing, ProShop ERP, Cetec ERP, xTuple, JobBOSS |
High-Tier | 100–500 employees | $35,000–$120,000 | Aptean Furniture ERP, Acumatica Manufacturing Edition, Infor CloudSuite Industrial (Syteline), Epicor, ECI M1 |
Enterprise Tier | 500+ employees | $120,000–$500,000+ | SAP S/4HANA for Manufacturing, Oracle Fusion Cloud ERP, Microsoft Dynamics 365 Finance & Operations |
ERP Software Integrations
Many furniture businesses rely on multiple software solutions to run. One common integration is ERP software, which balances manufacturing operations and day-to-day business processes. These solutions also typically include features like human resources, accounting, and CRM to help manage backend tasks. ERP systems with manufacturing modules offer material requirements planning, sales order management, quality management, and more.
Feature | Functionality |
---|---|
Accounting | Track revenue from sales orders and open invoices, as well as business expenses and payments to vendors. |
MRP | Streamline manufacturing with shop floor control, purchase planning, demand forecasting, and equipment maintenance scheduling. |
Customer Relationship Management (CRM) | Store customer contact information and order histories. Automate order entry, shipping notifications, and order status updates, as well as marketing emails based on purchase history. |
Human Resources | Manage the hiring and onboarding process, employee recruitment, track time and attendance, and benefits administration. |
Budgeting and Forecasting | Create estimates of the business’s future revenue and expenses based on historical trends and future market condition predictions. |
Furniture manufacturers that offer direct-to-consumer sales can use ERP to streamline the sales process. Some software solutions offer e-commerce functionality that allows your business to sell to consumers online. The system makes it easy to update pricing, add product variants, upload product images, and automatically update inventory quantities.
Many ERP systems can integrate with other solutions to cater to your unique business needs. Advanced ERP software sometimes includes business intelligence (BI) tools so furniture manufacturers can make better business decisions based on both financial and non-financial data. This information can help you find where improvements can be made to increase customer satisfaction.
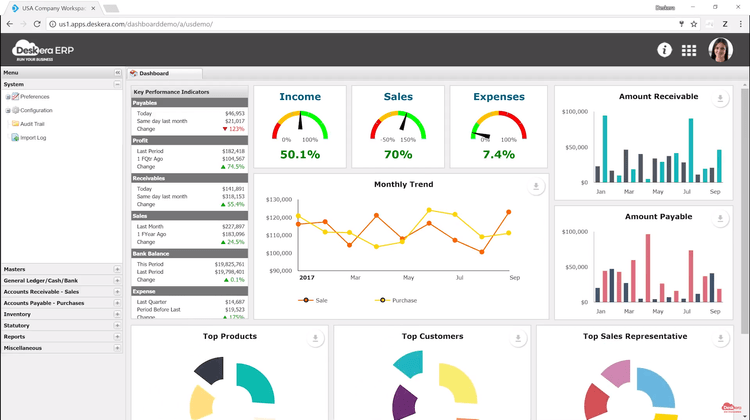
Other important software integrations for the furniture manufacturing industry include:
Inventory Management
Inventory management helps furniture manufacturing businesses track quantities and prices of raw materials, hardware, and finished products. Raw materials can include anything used to manufacture the furniture, such as screws, brackets, and nails. Purchase orders can be automatically sent to your vendors and distributors before the materials or hardware runs out to reduce downtime.
An inventory management system allows you to track finished furniture within your store or warehouse. The system includes descriptions of each product, material makeup, and available product variants. RFID and barcode labels can be placed on raw materials, hardware pieces, and assembled furniture to streamline physical real-time inventory counts.
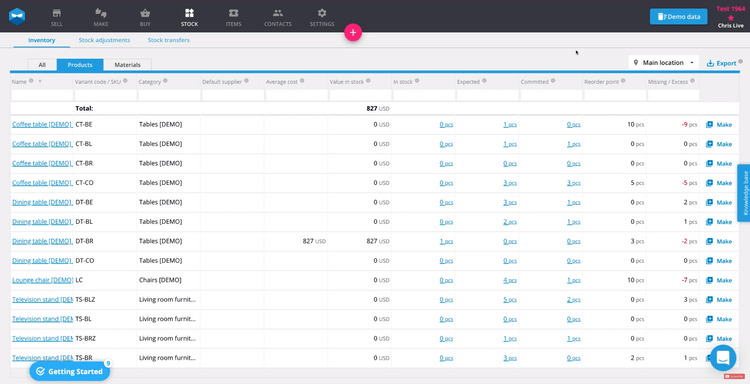
Production Planning
Production planning helps furniture manufacturers determine the materials, equipment, and labor requirements for each job order. If materials are low or out of stock, the system will warn you in advance so you can reorder as needed before beginning production.
The production schedule helps businesses track each piece of furniture throughout the manufacturing process. For example, you can see when the product is scheduled for the initial assembly and when the piece should move to the painting or finishing stage. This allows you to ensure products are being finished on schedule. If any part of the process is falling behind, corrective action can be taken to prevent late delivery.
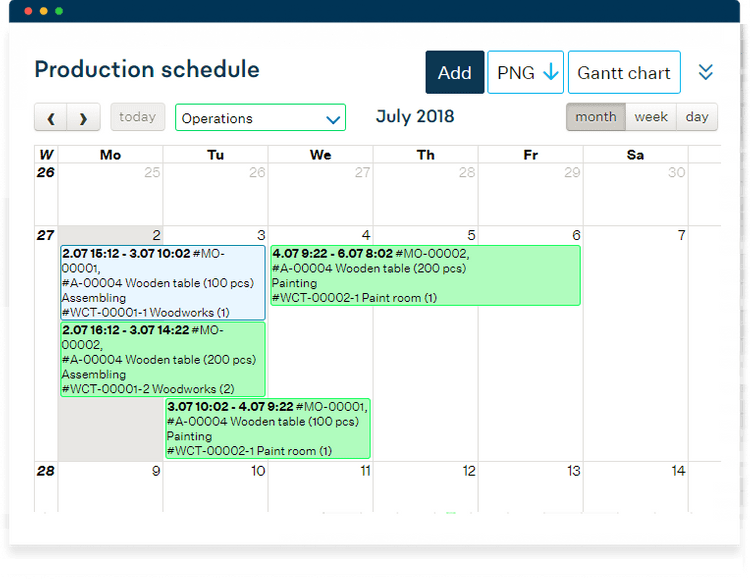
Product Configurator
Product configurators are commonly used for made-to-order and custom furniture sales. They allow customers to see how a completely customized piece of furniture will look. Specific parameters, including patterns, material type, and dimension limits, can be set up within the configurator to control what the customer can customize.
The product configurator will also provide real-time price quotes. The estimated cost will be calculated and presented automatically when the customer selects their desired customizations. The configurator will also show suggested add-ons and options to upsell products.
Finally, these products can be grouped together in the system to form furniture sets. For example, variations for a matching sofa, loveseat, and ottoman can have similar SKUs, so you can quickly find related products.
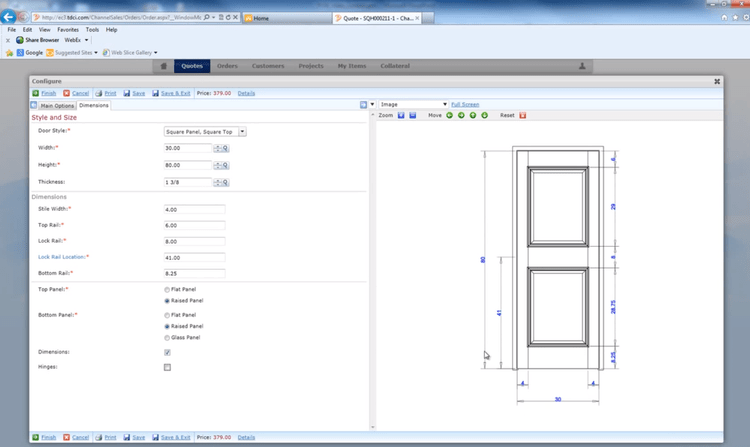